In today's rapidly evolving industrial landscape, organizations are constantly striving to find new ways to optimize their operations and enhance efficiency. One technology that has gained significant attention in recent years is the Internet of Things (IoT). When combined with predictive maintenance techniques, IoT has the potential to revolutionize how industries manage their assets and streamline their maintenance processes.
โ
Understanding Predictive Maintenance
โ
Maintenance has long been a critical aspect of any industrial operation. Traditionally, maintenance activities have been performed on a reactive basis, where equipment or machinery is repaired or replaced only after it fails. However, this approach can lead to costly downtime, decreased productivity, and increased expenses.
โ
Predictive maintenance, on the other hand, takes a proactive approach by leveraging data and analytics to predict when equipment failure is likely to occur. By monitoring various parameters such as temperature, vibration, and power consumption, IoT-enabled sensors can provide real-time insights into the health of assets.
โ
With the advent of the Internet of Things (IoT), predictive maintenance has become more accessible and efficient. IoT-enabled sensors can be easily installed on equipment, collecting and transmitting data to a centralized system. This data is then analyzed using advanced algorithms and machine learning techniques to identify patterns and anomalies that indicate potential failures.
โ
The Concept of Predictive Maintenance
โ
Predictive maintenance is based on the idea that equipment exhibits patterns or indicators of impending failure before a breakdown occurs. By collecting and analyzing data from sensors embedded in machinery, organizations can identify these patterns and take proactive measures to prevent failures.
โ
For example, an organization may notice that a particular machine tends to overheat before it fails. By monitoring the temperature readings from the sensors, they can set up alerts and triggers to notify maintenance personnel when the temperature exceeds a certain threshold. This allows them to take corrective actions, such as cleaning the cooling system or replacing faulty components, before a breakdown occurs.
โ
Furthermore, predictive maintenance can also help organizations optimize their maintenance activities. By analyzing the data collected from sensors, organizations can identify the optimal time for maintenance tasks, such as replacing parts or performing preventive maintenance. This not only reduces the risk of failures but also minimizes the impact on production schedules and reduces maintenance costs.
โ
โ
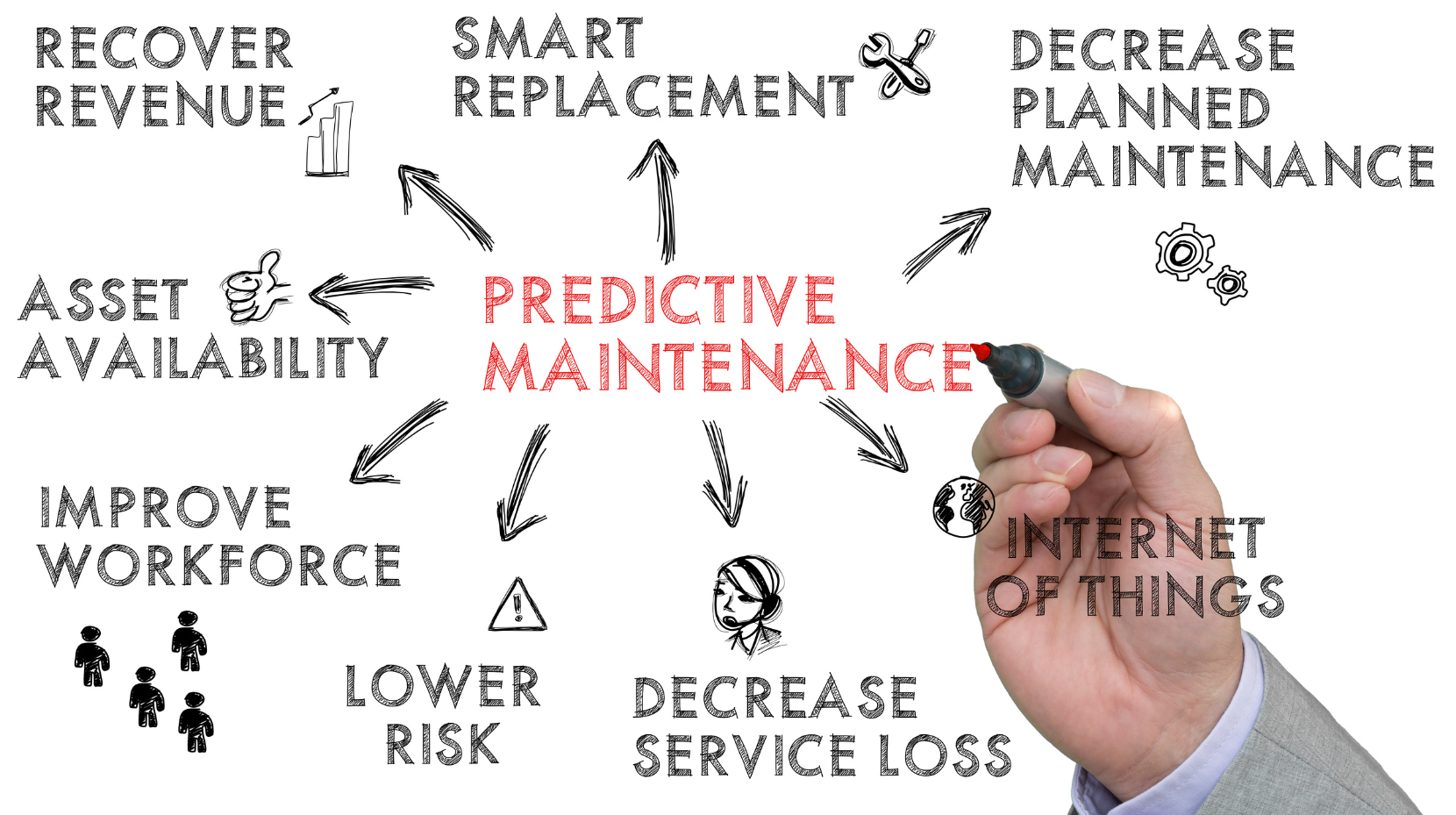
โ
โ
The Role of Predictive Maintenance in Industries
โ
Predictive maintenance plays a crucial role in various industries, including manufacturing, energy, transportation, and healthcare. By using IoT technology to monitor and analyze equipment health in real-time, organizations can minimize unplanned downtime, extend the lifespan of assets, and optimize maintenance schedules.
โ
In the manufacturing industry, for example, predictive maintenance can help prevent costly production interruptions. By continuously monitoring the performance of machines and analyzing the data, organizations can detect early signs of wear and tear, allowing them to schedule maintenance activities during planned downtime, rather than during critical production periods.
โ
In the energy sector, predictive maintenance can help optimize the performance of power plants and renewable energy installations. By monitoring parameters such as vibration and power consumption, organizations can identify potential issues, such as faulty bearings or inefficient components, and take corrective actions before they lead to equipment failures or energy losses.
โ
Transportation companies can also benefit from predictive maintenance. By monitoring the health of vehicles, such as trucks or trains, organizations can identify potential issues that may affect safety or reliability. This allows them to schedule maintenance activities during non-peak hours, minimizing disruptions to transportation services.
โ
In the healthcare industry, predictive maintenance can help ensure the reliability of critical medical equipment. By continuously monitoring parameters such as temperature and performance metrics, organizations can detect potential failures before they impact patient care. This allows them to schedule maintenance activities during periods of low patient demand, minimizing the risk of equipment failures during critical procedures.
โ
The Intersection of IoT and Predictive Maintenance
โ
IoT technology acts as a catalyst for predictive maintenance, enabling organizations to monitor and analyze data from a wide range of connected devices and sensors. This seamless integration of IoT with predictive maintenance techniques opens up a world of possibilities for enhancing efficiency and reducing costs.
โ
With the rapid advancement of technology, the Internet of Things (IoT) has emerged as a game-changer in the field of maintenance. By leveraging IoT, organizations can now move away from traditional reactive maintenance approaches and adopt a proactive and predictive approach. This shift has revolutionized the way assets are managed and maintained, leading to improved reliability, increased uptime, and significant cost savings.
โ
One of the key ways in which IoT enables predictive maintenance is by providing real-time visibility into the performance of assets. By connecting equipment and machinery to a network, organizations can collect and analyze vast amounts of data to detect anomalies and predict failures. This data-driven approach allows for proactive decision-making and targeted maintenance activities.
โ
Imagine a scenario where a manufacturing plant has hundreds of machines operating round the clock. Traditionally, maintenance teams would rely on manual inspections and periodic check-ups to identify potential issues. However, this reactive approach often resulted in unexpected breakdowns and costly downtime. With IoT-enabled predictive maintenance, sensors embedded in the machines continuously monitor various parameters such as temperature, vibration, and energy consumption. This real-time data is then transmitted to a central system where sophisticated algorithms analyze it to identify patterns and anomalies.
โ
By leveraging the power of machine learning and artificial intelligence, these algorithms can learn from historical data and predict when a machine is likely to fail. This allows maintenance teams to proactively schedule maintenance activities, replacing worn-out parts or addressing potential issues before they escalate. As a result, unplanned downtime is minimized, and the overall efficiency of the plant is significantly improved.
โ
โ
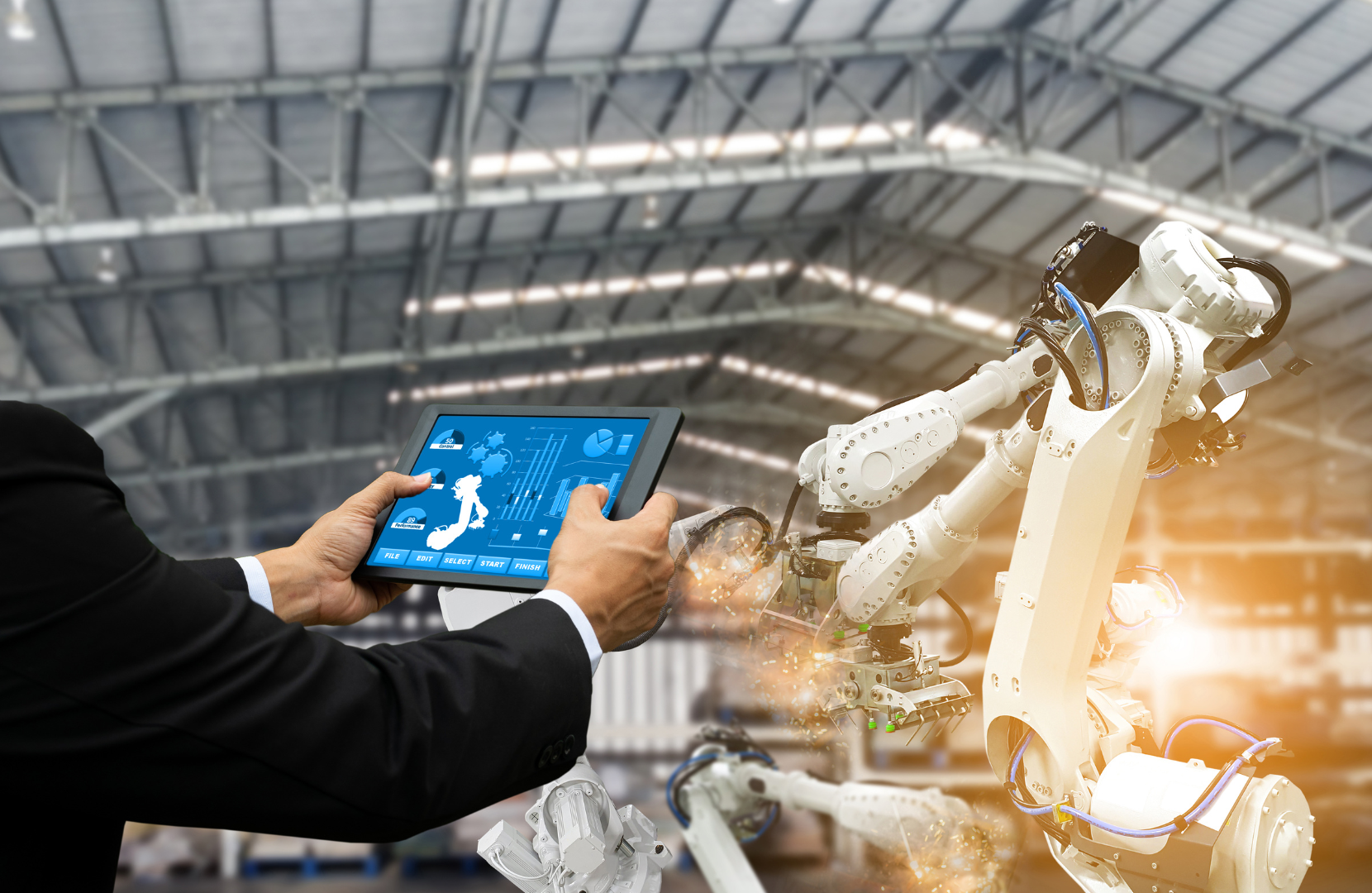
โ
โ
Key Components of IoT in Predictive Maintenance
โ
The key components of IoT in predictive maintenance include sensors, connectivity, data storage, and analytics. Sensors are responsible for collecting data related to equipment health, while connectivity ensures seamless communication between devices and systems. Data storage allows for the storage and retrieval of large volumes of data, and analytics algorithms analyze the data to extract meaningful insights.
โ
Sensors play a crucial role in the success of IoT-enabled predictive maintenance. These small devices are embedded in the equipment and are capable of capturing various parameters such as temperature, pressure, humidity, and vibration. They continuously monitor these parameters and transmit the data to a central system in real-time. This constant stream of data provides valuable insights into the health and performance of the assets, enabling organizations to make data-driven decisions.
โ
Connectivity is another critical component of IoT in predictive maintenance. It ensures that the sensors and devices can communicate with each other and with the central system seamlessly. This is achieved through various communication protocols such as Wi-Fi, Bluetooth, or cellular networks. The availability of reliable and robust connectivity is essential to ensure that the data is transmitted in real-time and without any interruptions.
โ
Data storage is another vital aspect of IoT in predictive maintenance. The amount of data generated by sensors can be enormous, especially in large-scale industrial settings. Therefore, organizations need robust and scalable data storage solutions to store and retrieve this data efficiently. Cloud-based storage solutions are often preferred as they provide flexibility, scalability, and easy accessibility to the data.
โ
Finally, analytics algorithms form the backbone of IoT-enabled predictive maintenance. These algorithms analyze the data collected from sensors and identify patterns, trends, and anomalies. By leveraging advanced statistical techniques and machine learning algorithms, organizations can extract meaningful insights from the data and predict when a failure is likely to occur. These insights enable maintenance teams to take proactive actions and optimize maintenance schedules, resulting in improved asset performance and reduced downtime.
โ
Benefits of IoT-Driven Predictive Maintenance
โ
The adoption of IoT-driven predictive maintenance offers numerous benefits to industrial operations, ranging from improved operational efficiency to reduced maintenance costs.
โ
Improving Operational Efficiency
โ
By leveraging IoT and predictive maintenance, organizations can minimize equipment downtime and optimize maintenance schedules. This results in increased operational efficiency, as assets are maintained at the optimal time, minimizing disruption to production processes.
โ
Reducing Maintenance Costs
โ
Traditional maintenance practices often involve routine or time-based checks, leading to unnecessary maintenance activities and increased costs. With IoT-enabled predictive maintenance, organizations can perform maintenance only when necessary, avoiding unnecessary expenses and minimizing the risk of equipment failure.
โ
Challenges in Implementing IoT-Based Predictive Maintenance
โ
While the potential benefits of IoT-driven predictive maintenance are significant, there are several challenges that organizations need to overcome in order to implement this approach successfully.
โ
Data Security and Privacy Concerns
โ
Collecting and analyzing vast amounts of data introduces security and privacy concerns. Organizations need to ensure that proper measures are in place to protect sensitive data and comply with relevant regulations. Robust encryption, access controls, and anonymization techniques can help mitigate these risks.
โ
โ
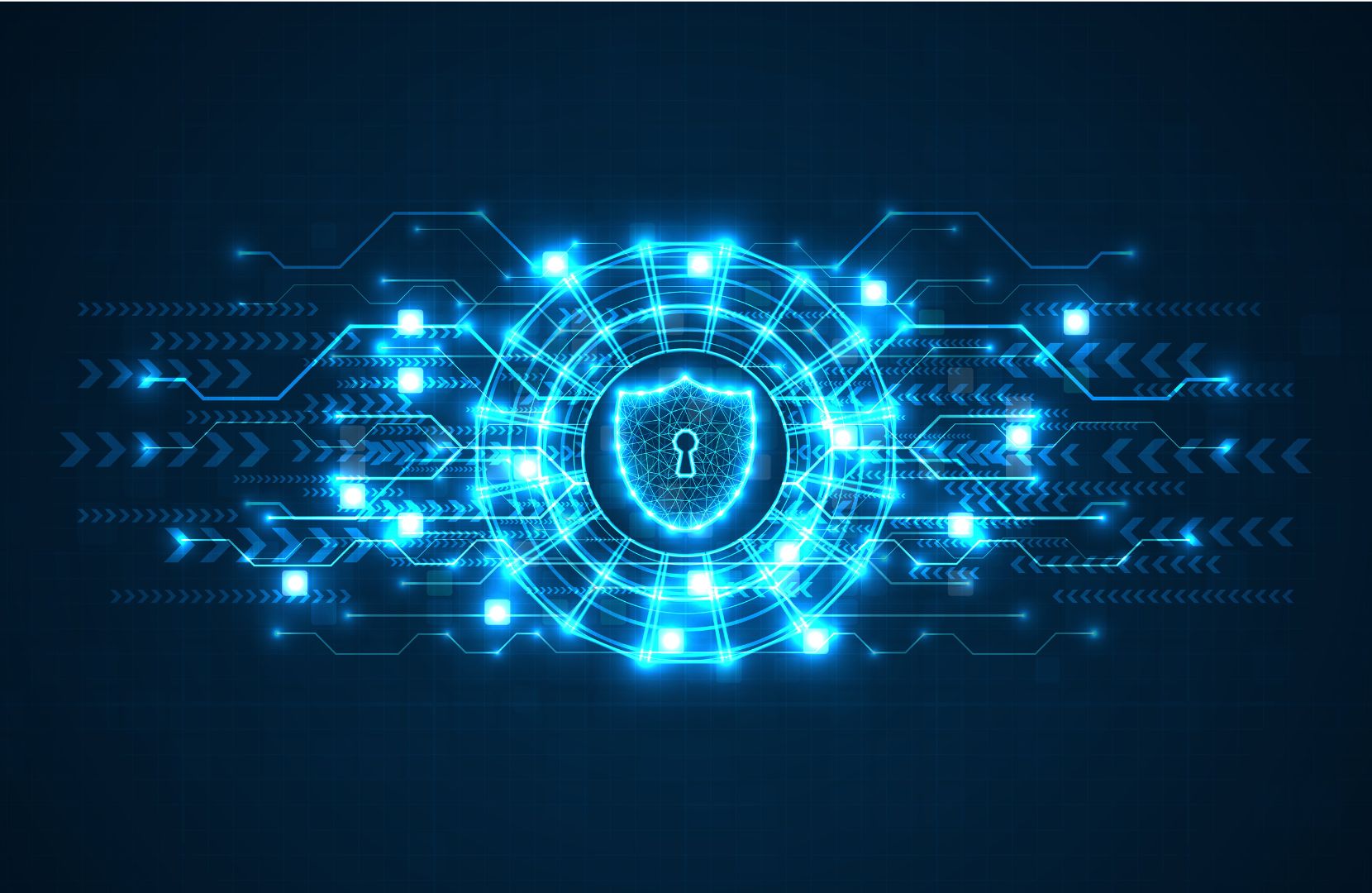
โ
โ
Integration with Existing Systems
โ
Integrating IoT with existing systems and processes can be complex and require significant investment. Organizations need to carefully plan and execute their integration strategies to ensure seamless compatibility and avoid disruptions to ongoing operations.
โ
The Future of Predictive Maintenance with IoT
โ
As technology continues to evolve, the future of predictive maintenance with IoT holds great promise. Emerging trends in IoT and predictive maintenance are set to transform industrial operations further.
โ
Emerging Trends in IoT and Predictive Maintenance
โ
Advancements in machine learning and artificial intelligence are enabling more accurate predictive models and more efficient maintenance practices. Additionally, edge computing, where data is processed near the source rather than in centralized servers, is gaining traction, allowing for real-time insights and faster response times.
โ
Potential Impact on Industrial Operations
โ
The potential impact of IoT-driven predictive maintenance on industrial operations is significant. By leveraging real-time data and predictive analytics, organizations can move from reactive to proactive maintenance approaches and optimize their asset management strategies. This can lead to increased productivity, reduced costs, and improved overall operational efficiency.
โ
As the industrial landscape continues to evolve, organizations are recognizing the importance of integrating IoT and predictive maintenance to enhance efficiency and stay ahead of the competition. By embracing these technologies and leveraging the benefits they offer, organizations can unlock new levels of operational excellence and drive sustained success in their respective industries.