3D printing is revolutionizing the way products are designed and manufactured. One of the most innovative and versatile techniques in this field is Selective Laser Sintering (SLS). By harnessing the power of lasers and powdered materials, SLS has emerged as a game-changer in the 3D printing industry.
Understanding the Basics of 3D Printing
Before delving into the intricacies of SLS, it is crucial to grasp the fundamentals of 3D printing. This revolutionary technology allows objects to be created layer by layer, based on digital models. Unlike traditional manufacturing methods, which involve subtractive processes like drilling or cutting, 3D printing is an additive process, where materials are built up to form the final product.
Over the years, 3D printing has witnessed a remarkable evolution, from its humble beginnings as a prototyping tool to a technology capable of fabricating complex structures with remarkable precision.
The Evolution of 3D Printing
When 3D printing first emerged in the 1980s, it was primarily used for rapid prototyping. Designers and engineers could quickly transform their ideas into physical prototypes, allowing for faster iteration and product development. This breakthrough innovation revolutionized the manufacturing industry, enabling companies to save time and resources in the product development process.
As the technology advanced, it found applications in various industries, including aerospace, automotive, and healthcare. In aerospace, 3D printing has been used to create lightweight yet strong components for aircraft, reducing fuel consumption and improving overall performance. In the automotive industry, 3D printing has enabled the production of custom parts and prototypes, accelerating the design and testing phase. In healthcare, 3D printing has opened up new possibilities in personalized medicine, allowing for the creation of patient-specific implants and prosthetics.
Today, 3D printers have become more accessible and affordable, paving the way for widespread adoption and innovation. From small-scale desktop printers to large industrial machines, businesses and individuals can now harness the power of 3D printing to create customized products. This democratization of manufacturing has empowered entrepreneurs and makers to bring their ideas to life, fostering a culture of innovation and creativity.
Key Components of a 3D Printer
A 3D printer is composed of several crucial components that work together to transform digital designs into physical objects. Understanding these components is essential for anyone looking to explore the world of 3D printing:
- The Build Platform: This is the platform on which the object is built layer by layer. It provides a stable foundation for the printing process and ensures the accuracy of each layer.
- Print Head or Extruder: The print head deposits or extrudes the material, following the digital design's specifications. It heats the material to its melting point and precisely controls its flow, allowing for the creation of intricate shapes and structures.
- Control System: The control system coordinates the movements and operations of the printer to ensure the accurate deposition of materials. It interprets the digital design file and translates it into specific instructions for the printer's motors and extruder.
- Power Source: The power source supplies the necessary energy to drive the printer's components, such as the motors and heating elements. It ensures a stable and consistent power supply, enabling uninterrupted printing.
- Filament or Resin: The material used for 3D printing, whether it is filament or resin, plays a crucial role in determining the final properties of the printed object. Different materials offer varying levels of strength, flexibility, and durability, allowing for a wide range of applications.
- Software: The software used in 3D printing is responsible for creating and editing digital designs, as well as preparing them for printing. It allows users to manipulate and customize their designs, adjusting parameters such as size, orientation, and infill density.
By understanding these key components, individuals can gain a deeper appreciation for the intricacies of 3D printing and explore the limitless possibilities it offers in terms of design, manufacturing, and innovation.
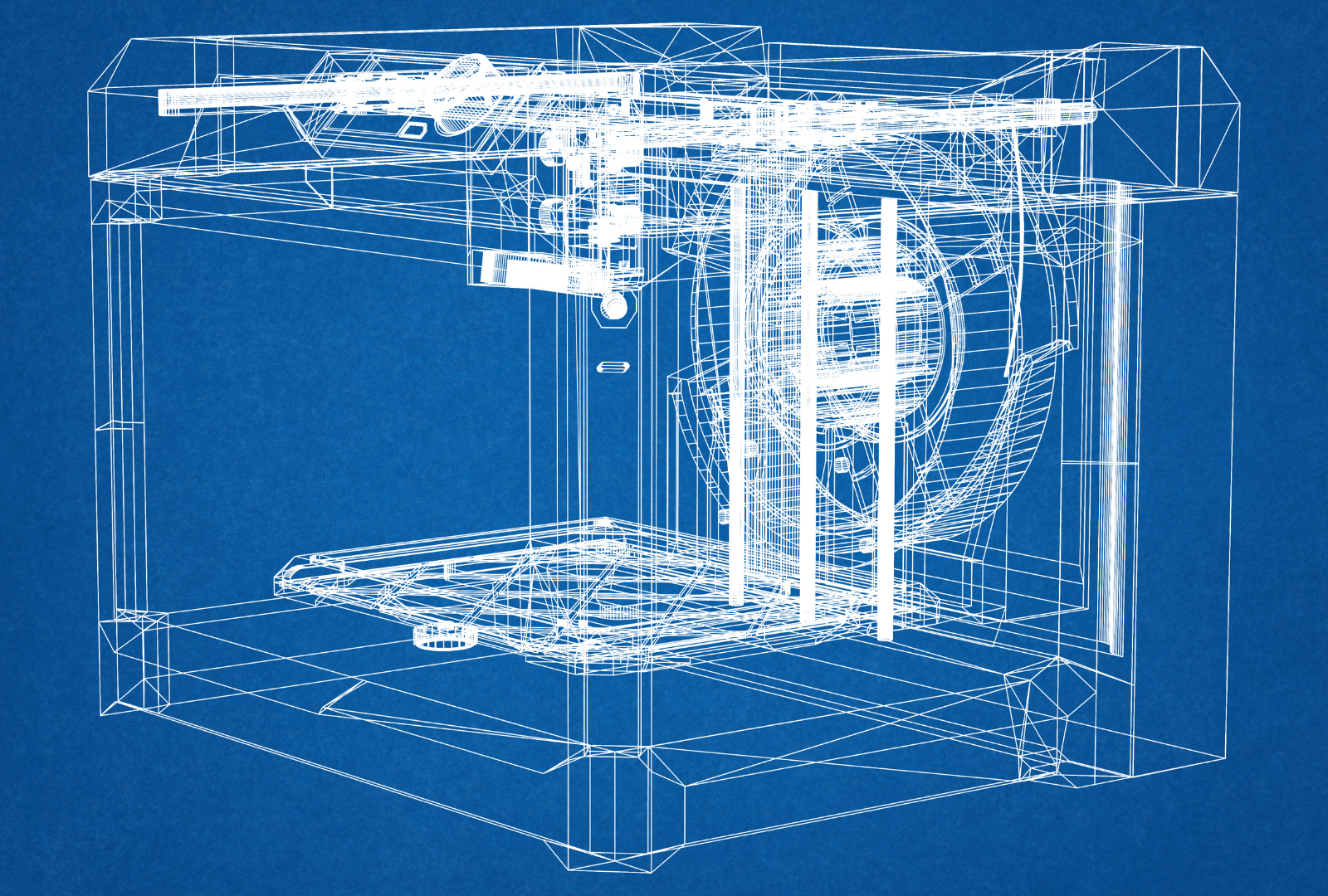
Introduction to Selective Laser Sintering (SLS)
Now that we have established a foundation in 3D printing, let's dive into the specifics of Selective Laser Sintering. SLS is a powder bed fusion 3D printing technique that utilizes lasers to selectively fuse powdered materials together, layer by layer, to create complex objects.
Compared to other 3D printing methods, such as Fused Deposition Modeling (FDM) or Stereolithography (SLA), SLS offers distinct advantages in terms of versatility and material capabilities.
How Does SLS Work?
SLS starts with a thin layer of powdered material spread across the build platform. A high-powered laser then selectively melts or sinters the powdered particles together, forming the desired shape. The build platform then lowers, and a new layer of powder is spread, repeating the process until the entire object is fabricated.
The use of lasers in SLS allows for precise control over the fusion process, resulting in highly accurate and detailed prints. Additionally, the ability to print self-supporting structures eliminates the need for support materials, making SLS ideal for intricate designs.
Let's take a closer look at the process. When the laser scans the powdered material, it creates localized heat, causing the particles to fuse together. The laser's intensity and duration are carefully controlled to ensure the right amount of heat is applied, resulting in a strong bond. As the build platform lowers, a roller or blade spreads a new layer of powder on top, ready for the next round of laser scanning. This layer-by-layer approach allows for the creation of complex geometries and intricate details that would be challenging to achieve with traditional manufacturing methods.
Another advantage of SLS is its ability to produce objects with good mechanical properties. The fusion of the powdered particles creates a solid, dense structure, resulting in parts that are strong and durable. This makes SLS suitable for a wide range of applications, including functional prototypes, end-use parts, and even medical implants.
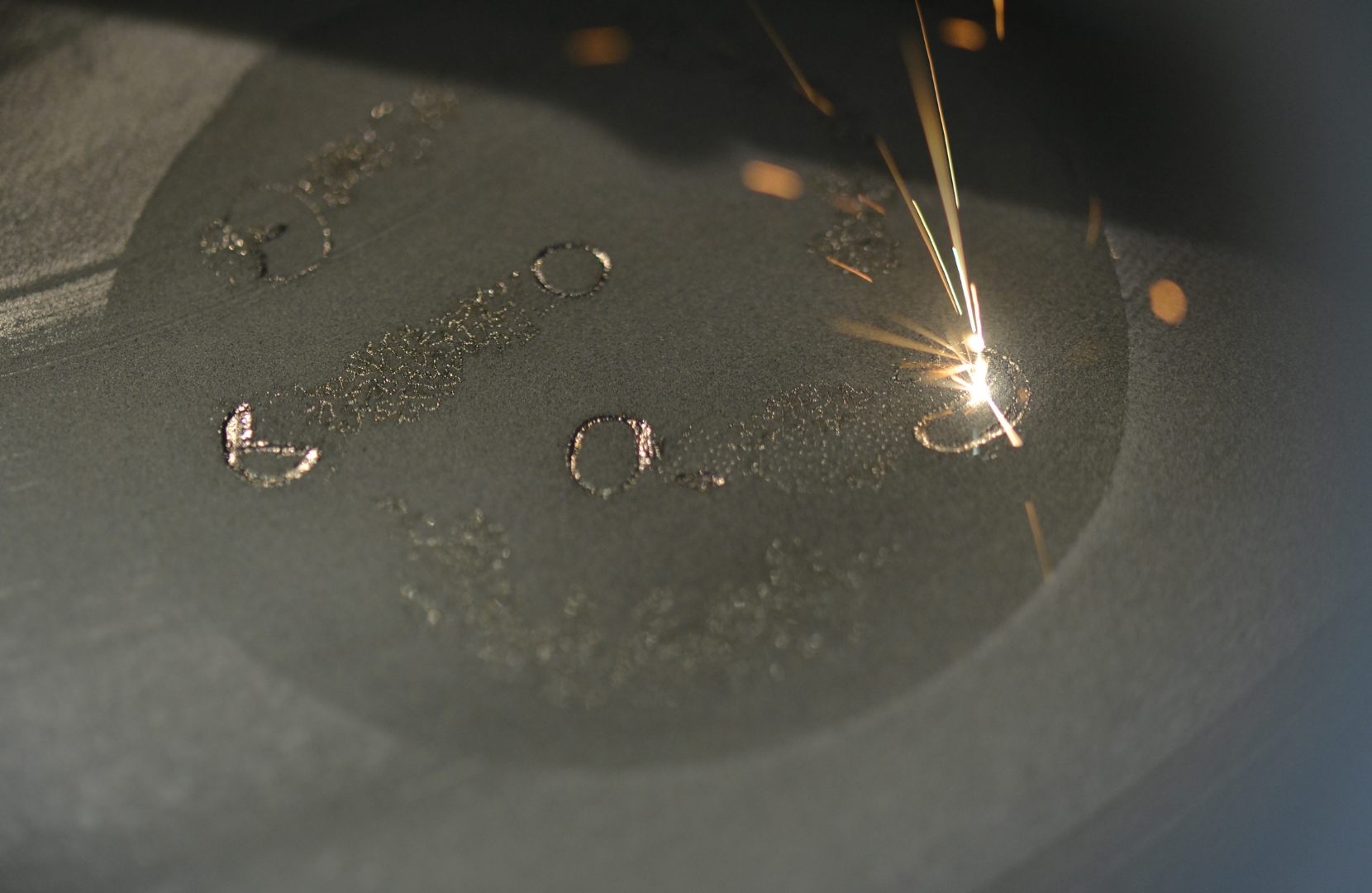
Materials Used in SLS
One of the significant advantages of SLS is its wide range of compatible materials. Unlike other 3D printing techniques that are limited to specific materials, SLS can work with a variety of powders, including plastics, metals, and ceramics.
Plastics commonly used in SLS include nylon, polycarbonate, and polypropylene. These materials offer excellent mechanical properties, making them suitable for functional prototypes and end-use parts. Nylon, in particular, is widely used in SLS due to its strength, flexibility, and heat resistance.
Metal powders, such as aluminum, titanium, and steel, can also be used in SLS, enabling the production of metal components with complex geometries. This opens up new possibilities in industries such as aerospace, automotive, and healthcare, where lightweight yet strong metal parts are in high demand.
In addition to plastics and metals, SLS can also work with ceramic powders. Ceramics offer unique properties such as high temperature resistance, electrical insulation, and biocompatibility, making them suitable for a wide range of applications, including electronics, aerospace, and medical devices.
It's worth noting that the choice of material for SLS depends on the specific requirements of the application. Factors such as mechanical properties, thermal stability, chemical resistance, and cost play a crucial role in material selection.
Comparing SLS to Other 3D Printing Techniques
While SLS shares similarities with other 3D printing techniques, it sets itself apart in terms of capabilities and applications. Let's take a closer look at how SLS compares to Fused Deposition Modeling (FDM) and Stereolithography (SLA).
SLS vs Fused Deposition Modeling (FDM)
FDM, one of the most widely used 3D printing techniques, involves extruding molten thermoplastic filaments to build objects layer by layer. While FDM is cost-effective and accessible, it is limited in terms of surface finish and material compatibility. SLS, on the other hand, offers better surface quality and material versatility, making it suitable for a wider range of applications.
SLS vs Stereolithography (SLA)
SLA relies on photopolymerization to create objects by selectively curing liquid resin with a UV laser. SLA produces high-resolution prints with smooth surfaces, but it is limited by the need for support structures and the availability of compatible resins. SLS, with its ability to print self-supporting structures and work with a greater variety of materials, overcomes these limitations.
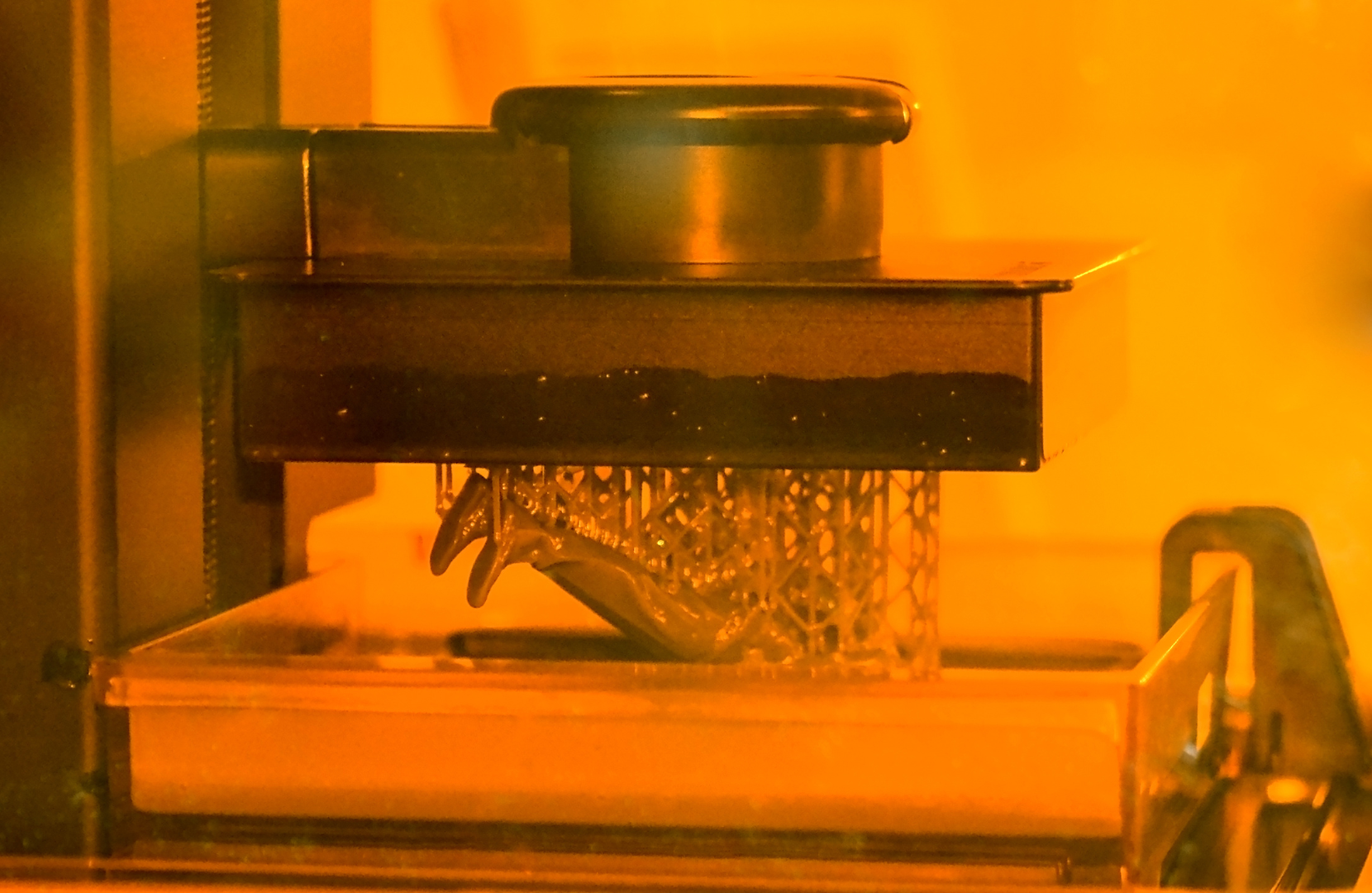
The Advantages of Selective Laser Sintering
Now that we understand the inner workings of SLS and its comparison to other 3D printing techniques, let's explore its unique advantages that make it a game-changer.
Superior Detail and Precision
SLS delivers exceptional detail and precision, thanks to the high-powered lasers used in the process. The lasers can achieve resolutions as fine as 25 microns, resulting in accurate and intricate prints. This level of precision makes SLS suitable for applications that demand tight tolerances and intricate features.
Greater Material Versatility
Unlike other 3D printing techniques, SLS is not limited to a specific range of materials. With SLS, it is possible to work with various powdered materials, enabling the creation of functional prototypes, end-use parts, and even custom-made products. This versatility allows businesses and designers to explore different materials and optimize their designs for specific purposes.
Applications of SLS in Various Industries
With its unique strengths, SLS finds applications in various industries, providing innovative solutions and pushing the boundaries of traditional manufacturing processes. Let's explore some key areas where SLS is making a significant impact.
SLS in the Medical Field
SLS has revolutionized the medical field by enabling the production of customized prosthetics, orthotics, and implants. The ability to print complex geometries and incorporate patient-specific designs has transformed the way medical devices are created. SLS also facilitates the rapid prototyping of surgical tools and anatomical models, allowing for better surgical planning and training.
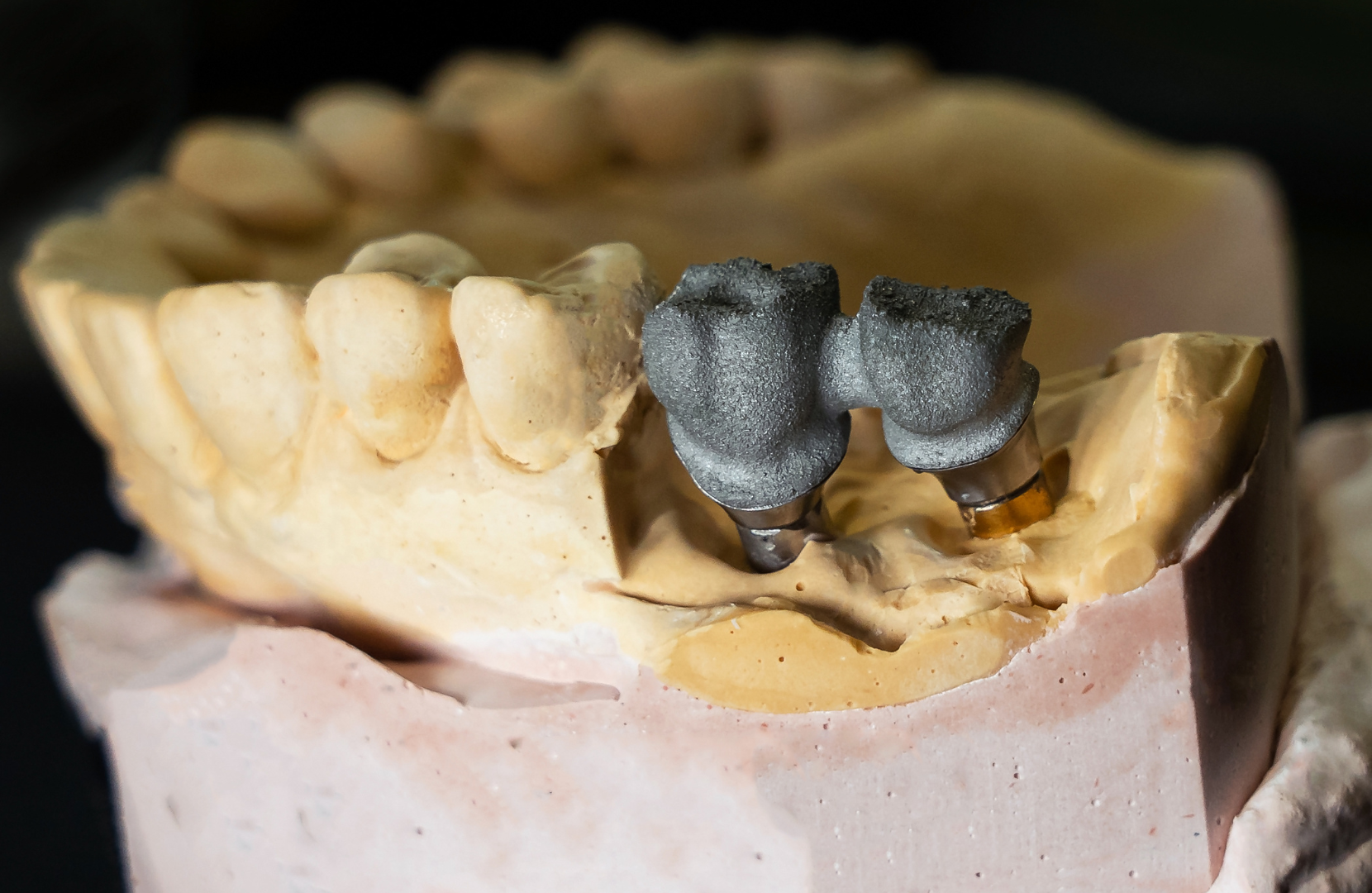
SLS in Automotive Manufacturing
The automotive industry has embraced SLS for its ability to produce lightweight components with intricate designs. SLS enables the creation of complex air ducts, conformal cooling channels, and functional prototypes that can withstand testing and validation processes. With SLS, manufacturers can reduce tooling costs, improve product performance, and accelerate their product development cycles.
Conclusion
Selective Laser Sintering (SLS) has emerged as a game-changer in the 3D printing industry. By leveraging lasers and powdered materials, SLS offers superior detail, precision, and material versatility. With applications in various industries, SLS continues to push the boundaries of traditional manufacturing processes. As technology advances and materials evolve, SLS is poised to shape the future of manufacturing, paving the way for innovative and customized products.