3D Systems is widely recognized as a trailblazer in the field of additive manufacturing. This groundbreaking technology has revolutionized the way we design and create objects, with 3D Systems leading the charge. In this article, we will take a deep dive into the birth of 3D Systems, their contributions to additive manufacturing, as well as case studies showcasing their success in various industries. We will also explore the future of 3D Systems and the potential challenges they may face.
The Birth of 3D Systems
Before delving into the present and future of 3D Systems, it is vital to understand their humble beginnings. Founded in 1986 by Chuck Hull, the inventor of stereolithography, and his team of visionaries, 3D Systems emerged with a bold mission to change the way manufacturing is approached.
Chuck Hull, a brilliant engineer and inventor, had a deep passion for exploring new possibilities. He was driven by a relentless curiosity and a desire to push the boundaries of what was thought possible. It was this drive that led him to develop the groundbreaking technology of stereolithography, a process that allowed for the creation of three-dimensional objects from digital designs.
With the invention of stereolithography, Hull and his team saw the potential to revolutionize the world of manufacturing. They recognized that this technology had the power to bridge the gap between imagination and reality, allowing individuals and industries alike to bring their ideas to life with unprecedented precision and efficiency.
However, the journey was not without its challenges. In the early years, 3D Systems faced numerous setbacks and obstacles. The technology was still in its infancy, and there were many skeptics who doubted its potential. But Hull and his team remained undeterred. They believed in the transformative power of 3D printing and were determined to overcome any obstacles that stood in their way.
Through their perseverance and dedication, the team at 3D Systems made breakthrough after breakthrough. They constantly pushed the boundaries of what was possible, refining and improving their technology with each iteration. They worked tirelessly to develop new materials, expand the capabilities of their printers, and find innovative solutions to the challenges they faced.
Their efforts paid off, and 3D Systems soon became a leader in the field of additive manufacturing. Their printers were adopted by industries across the globe, revolutionizing the way products were designed and manufactured. From aerospace to healthcare, from automotive to consumer goods, 3D Systems' technology was making a profound impact.
Today, 3D Systems continues to innovate and push the boundaries of what is possible with 3D printing. They are constantly developing new materials, expanding their range of printers, and exploring new applications for their technology. With each passing year, they bring us closer to a future where 3D printing is an integral part of our everyday lives.
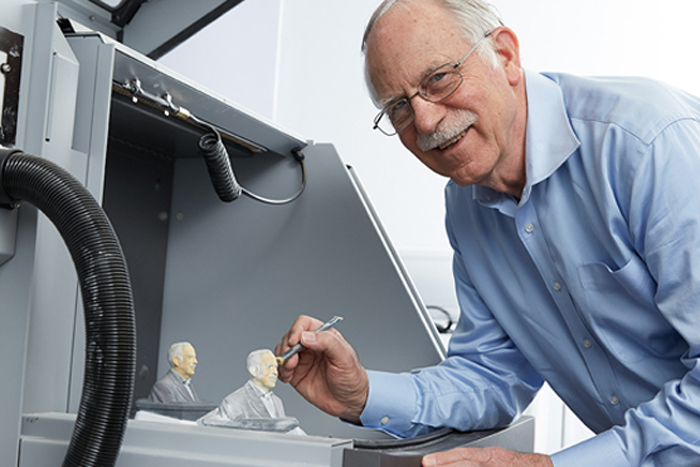
Understanding Additive Manufacturing
Before we delve further into 3D Systems' contributions, it is crucial to grasp the fundamentals of additive manufacturing. Specifically, we will take a closer look at the basics of 3D printing and how this innovative technology has evolved over time.
The Basics of 3D Printing
At its core, 3D printing involves the creation of a three-dimensional object from a digital design file. This process occurs layer by layer, with the printer depositing material onto a build platform based on the specifications outlined in the design file. From plastics to metals and even biological materials, the range of materials used in 3D printing continues to expand, enabling remarkable possibilities.
3D printing offers unrivaled flexibility and customization. No longer bound by traditional manufacturing constraints, designers and engineers can bring their ideas to fruition with intricate details and complex geometries that were once unimaginable. This freedom of design has propelled progress in numerous fields, from medicine and aerospace to consumer goods and beyond.
The Evolution of Additive Manufacturing
Since its inception, additive manufacturing has undergone remarkable advancements. What started as a niche technology with limited applications has transformed into a multidimensional toolkit for innovation.
3D Systems played a pivotal role in this evolution, continually pushing the boundaries of what is possible. Through their tireless research and development efforts, they have pioneered breakthroughs in materials, software, and hardware, making 3D printing more accessible, efficient, and precise.
With each passing year, additive manufacturing technologies continue to mature, providing an ever-expanding array of possibilities for industries worldwide. 3D Systems has been at the forefront of these advancements, catalyzing innovation across numerous fields.
.png)
3D Systems' Contributions to Additive Manufacturing
Now that we have gained a solid understanding of additive manufacturing, it is time to explore how 3D Systems has contributed to this revolutionary field.
Innovative Products and Solutions
3D Systems has consistently introduced pioneering products and solutions that have propelled the field of additive manufacturing forward. From high-performance industrial 3D printers to advanced software platforms, their offerings have always pushed the envelope and set new industry standards.
By continually refining their technology and listening to customer feedback, 3D Systems has been able to address the unique challenges faced by industries across the globe. By delivering tailored solutions, they have helped businesses optimize production processes, reduce costs, and unlock new possibilities for product development.
Impact on Various Industries
3D Systems' innovative applications have extended far beyond traditional manufacturing. Their impact can be seen across an array of industries, driving breakthroughs and transforming outdated practices.
In the medical field, 3D Systems has revolutionized patient care through personalized healthcare solutions. By leveraging 3D printing, medical professionals can create anatomically accurate models, surgical guides, and even patient-specific implants. This technology has not only improved surgical outcomes but also enabled faster and more cost-effective treatment.
In the automotive industry, 3D Systems' contributions have been equally impactful. The ability to rapidly prototype and iterate designs has accelerated the development process, ensuring vehicles reach the market faster. Additionally, additive manufacturing has allowed automotive designers to push the boundaries of vehicle performance, creating lighter and more efficient components that enhance fuel efficiency and safety.
Case Studies of 3D Systems' Success
Seeing 3D Systems' contributions in action can provide valuable insights into the real-world impact of additive manufacturing. Let's explore two compelling case studies that showcase their success in different industries.
Medical Field Applications
In the medical field, 3D Systems' technology has transformed the way surgeries are approached. Through the use of 3D-printed anatomical models, surgeons can meticulously plan procedures beforehand, reducing operative time and enhancing patient safety. These realistic models allow surgeons to accurately assess complex cases and explore innovative approaches.
Furthermore, 3D Systems' expertise in additive manufacturing has enabled the creation of patient-specific implants. These custom implants perfectly suit individual patient needs, optimizing implant-tissue interaction for improved outcomes and reduced recovery time. The ability to personalize medical devices has the potential to revolutionize patient care, offering tailored solutions that were once unimaginable.
.png)
Automotive Industry Innovations
In the automotive industry, 3D Systems has collaborated with leading manufacturers to drive innovation and enhance performance. One notable partnership involved the development of lightweight components using advanced materials and design optimization techniques.
By leveraging the freedom of design offered by additive manufacturing, 3D Systems and their automotive partners were able to create complex geometries that improved aerodynamics and fuel efficiency. This collaboration resulted in cars that consumed less energy while delivering enhanced performance, proving that additive manufacturing has practical applications beyond prototyping.
.png)
The Future of 3D Systems and Additive Manufacturing
As we look ahead, it is clear that 3D Systems will continue to shape the future of additive manufacturing. With a steadfast commitment to innovation and a track record of success, they are well-positioned to overcome the challenges of tomorrow.
Upcoming Projects and Plans
3D Systems has a robust pipeline of projects and plans that promise to push the boundaries of what additive manufacturing can achieve. Ongoing research and development efforts aim to further enhance the speed, precision, and versatility of 3D printing technologies.
In addition to technological advancements, 3D Systems is continuously expanding their materials portfolio, focusing on developing new materials that cater to diverse industry requirements. By offering a wide range of materials, they strive to address the unique needs of industries ranging from aerospace to consumer goods.
Predictions and Potential Challenges
While the future looks promising for 3D Systems and additive manufacturing, it is essential to acknowledge the potential challenges that lie ahead. As the technology becomes more prevalent, regulatory frameworks and intellectual property concerns may come to the forefront, requiring innovative solutions and collaboration across industries.
Moreover, the quest for sustainable and environmentally friendly manufacturing practices will likely shape the future of additive manufacturing. 3D Systems is well aware of this challenge and is actively exploring ways to minimize environmental impact and promote responsible manufacturing processes.
Conclusion
3D Systems has played a pivotal role in revolutionizing additive manufacturing. Through their visionary leadership, innovative products, and impactful applications, they have transformed industries and empowered individuals worldwide. With a clear path ahead and the dedication to overcome challenges, 3D Systems is poised to shape the future of manufacturing as we know it.