3D printing technology has come a long way since its inception. From creating simple objects to fabricating complex and intricate designs, it has revolutionized various industries. But as technology advances, so does the need for more efficient and cost-effective printing techniques. Enter binder jetting, a 3D printing method that is making waves in the manufacturing world. In this article, we will explore the basics of 3D printing, the science behind binder jetting, its advantages and limitations, its applications in different industries, and the future prospects of this cutting-edge technique.
Understanding the Basics of 3D Printing
Before we dive into the world of binder jetting, let's take a moment to understand the fundamentals of 3D printing. 3D printing, also known as additive manufacturing, is a process of creating three-dimensional objects by layering materials on top of each other. Unlike traditional methods of manufacturing, which involve subtractive processes like cutting and drilling, 3D printing builds objects from the ground up, layer by layer.
3D printing has revolutionized the manufacturing industry, offering numerous benefits and possibilities. One of the key advantages of 3D printing is its ability to create complex geometries that would be difficult or impossible to achieve with traditional methods. This opens up new opportunities for product design and innovation.
Another advantage of 3D printing is its ability to create customized objects. Traditional manufacturing methods often require expensive tooling and setup costs, making it impractical to produce small quantities of custom-designed products. With 3D printing, however, each object can be individually designed and produced, allowing for personalization and customization on a mass scale.
The Evolution of 3D Printing Technologies
Over the years, various 3D printing technologies have emerged, each with its own set of advantages and limitations. From stereolithography (SLA) to fused deposition modeling (FDM), these techniques have opened new doors for rapid prototyping, customization, and small-scale production. However, as the demand for larger-scale production and faster printing speeds grows, a new player has entered the field: binder jetting.
Stereolithography (SLA) was one of the earliest 3D printing technologies to be developed. It works by curing liquid photopolymers using a UV laser, creating solid layers that build up to form the final object. SLA is known for its high level of detail and accuracy, making it ideal for creating intricate prototypes and models.
Fused deposition modeling (FDM), on the other hand, works by extruding thermoplastic filaments layer by layer to create the object. This method is widely used due to its affordability and ease of use. FDM printers are commonly found in homes, schools, and small businesses, enabling users to bring their ideas to life.
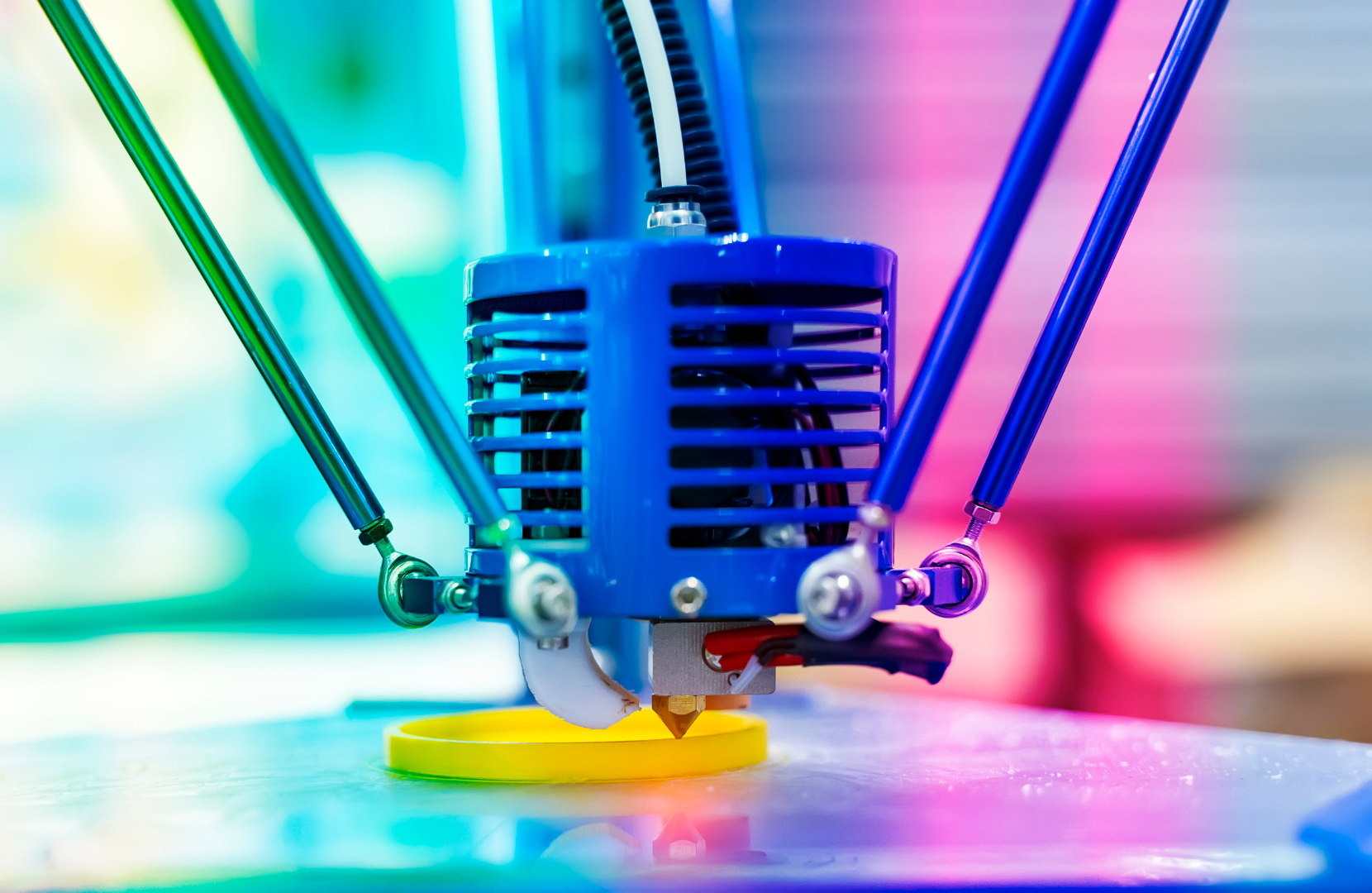
What is Binder Jetting?
Binder jetting is a 3D printing technique that uses a liquid binder to bond layers of powder material together. Unlike other methods where the material is directly melted or cured to form the object, binder jetting relies on the binding agent to create a solid structure. This unique approach allows for faster printing speeds and the ability to use a wide range of materials.
Binder jetting offers several advantages over other 3D printing technologies. One of the key benefits is its ability to print large-scale objects. Traditional 3D printing methods often have limitations in terms of build size, but binder jetting can overcome these limitations, making it suitable for architectural models, industrial prototypes, and even full-scale production.
Another advantage of binder jetting is its versatility in material selection. While some 3D printing technologies are limited to specific materials, binder jetting can work with a wide range of powders, including metals, ceramics, and even sand. This opens up possibilities for creating objects with unique properties, such as lightweight metal components or heat-resistant ceramic parts.
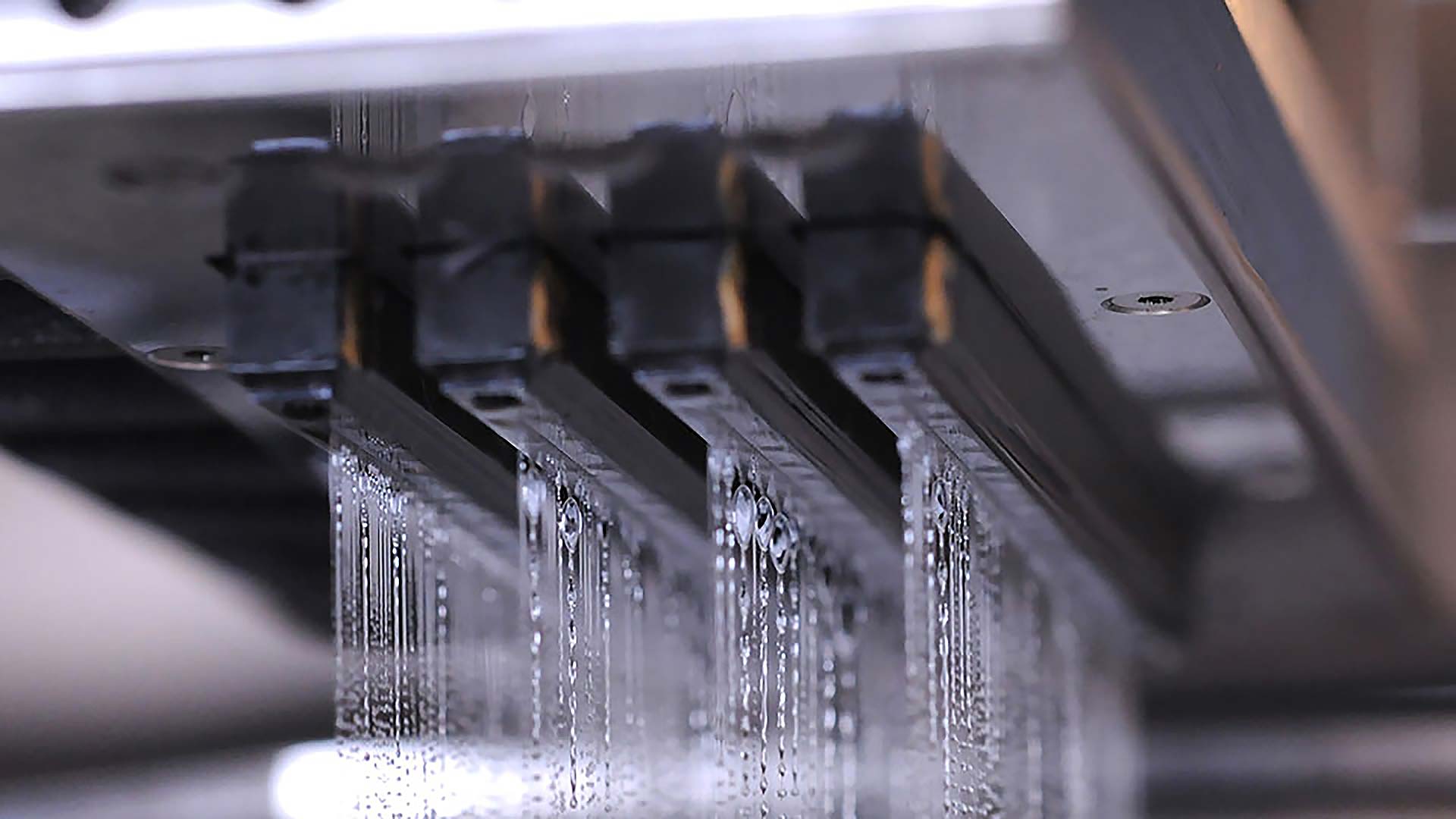
The Science Behind Binder Jetting
Now that we have a basic understanding of 3D printing and binder jetting, let's explore the science behind this innovative technique. Binder jetting involves a precise and controlled process that transforms loose powder into a solid object. Here's how it works:
Binder jetting, a cutting-edge 3D printing technique, combines the principles of material science, engineering, and computer programming to create intricate and complex objects. This process revolutionizes manufacturing by enabling the production of customized, high-quality products in a cost-effective and time-efficient manner.
The Process of Binder Jetting
The binder jetting process begins with a thin layer of powder spread evenly across a build platform. This powder can be composed of various materials such as metals, ceramics, or polymers, depending on the desired end product. The even distribution of the powder layer is crucial for achieving accurate and consistent results.
Once the powder layer is prepared, a printhead equipped with tiny nozzles moves across the build platform. The printhead precisely jets fine droplets of a liquid binder onto the powder layer, selectively binding it together. The binder acts as a temporary adhesive, holding the powder particles in place and forming the desired shape.
This process is repeated layer by layer, with each subsequent layer being spread and selectively bound to the previous one. The precise deposition of the binder ensures the creation of intricate geometries and complex internal structures that were previously unattainable with traditional manufacturing methods.
Once the printing is complete, the object is carefully removed from the build platform. However, the object is not yet ready for use as it undergoes post-processing to enhance its mechanical properties and surface finish.
Post-processing techniques may include curing, debinding, and sintering. Curing involves exposing the object to heat or UV light to strengthen the binder and solidify the structure. Debinding is the removal of excess binder from the object, often through chemical or thermal processes. Finally, sintering involves subjecting the object to high temperatures, causing the powder particles to fuse together and create a dense, solid object.
Materials Used in Binder Jetting
Binder jetting offers a wide variety of materials to choose from. Metals, ceramics, and polymers can all be used in this printing technique. The ability to work with different materials opens up endless possibilities for applications in diverse industries, ranging from automotive and aerospace to healthcare and fashion.
Metal powders, such as stainless steel, titanium, and aluminum, are commonly used in binder jetting for their excellent mechanical properties and durability. These materials find applications in the production of automotive parts, aerospace components, and even jewelry.
Ceramic powders, such as zirconia and alumina, are utilized for their high heat resistance, electrical insulation, and biocompatibility. They are often employed in the manufacturing of dental implants, cutting tools, and electronic components.
Polymers, including various types of plastics, are also compatible with binder jetting. This allows for the creation of lightweight and flexible objects, making them suitable for applications in the fashion industry, consumer goods, and medical devices.
As technology advances, researchers and engineers continue to explore new materials that can be used in binder jetting. This ongoing development expands the possibilities of what can be achieved through this innovative 3D printing technique.
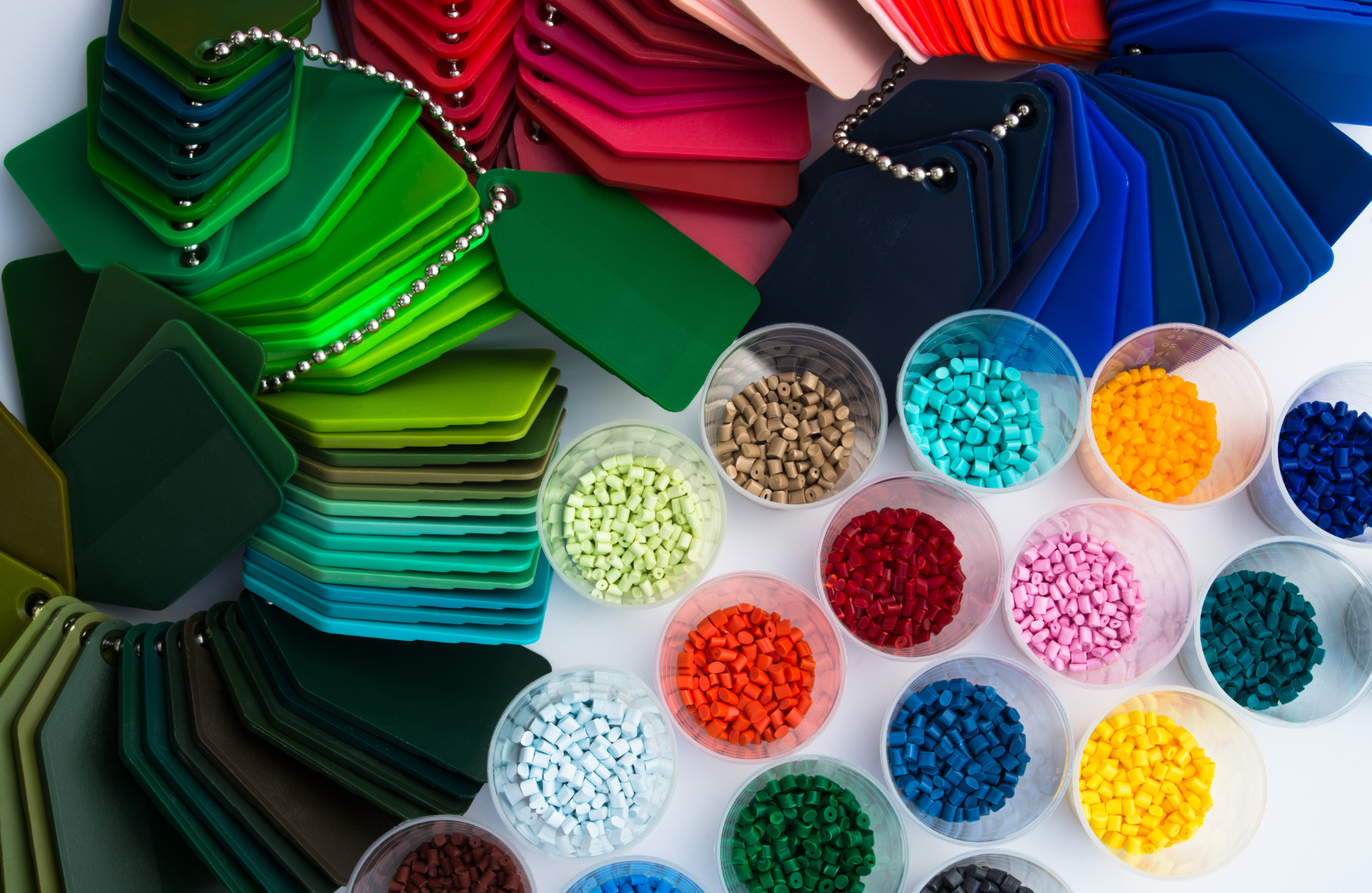
Comparing Binder Jetting to Other 3D Printing Techniques
While binder jetting has its unique advantages, it is essential to understand how it compares to other 3D printing techniques. Let's take a look:
Advantages of Binder Jetting
- High printing speeds: Binder jetting can achieve faster printing speeds compared to other methods, making it ideal for large-scale production.
- Material versatility: This technique works with a wide range of materials, giving designers and engineers the flexibility to choose the most suitable material for their application.
- Cost-effective: Binder jetting is often more cost-effective compared to other 3D printing methods, making it a preferred choice for businesses looking to optimize their production processes.
Limitations of Binder Jetting
- Lower resolution: Compared to other techniques like SLA or FDM, binder jetting may have lower resolution, which means objects may not have the same level of intricate detail.
- Post-processing requirements: Objects printed through binder jetting often require additional post-processing steps, such as curing, debinding, or sintering, which can add time and cost to the overall production process.
Applications of Binder Jetting in Various Industries
Binder jetting's unique features make it suitable for a wide range of industries. Here are two examples of how binder jetting is being used:
Binder Jetting in the Automotive Industry
In the automotive industry, binder jetting is opening doors to new possibilities for lightweight yet durable components. From engine parts to custom tooling, this technique allows for complex geometries and on-demand manufacturing, reducing production time and costs.
Use of Binder Jetting in Healthcare
Binder jetting has also found its way into the healthcare industry. It enables the production of patient-specific implants, prosthetics, and dental models, revolutionizing personalized medicine and improving patient outcomes.
The Future of 3D Printing: Is it Binder Jetting?
With its unique advantages and growing application areas, binder jetting is undoubtedly shaping the future of 3D printing. Ongoing research and developments are further enhancing this technology's capabilities, addressing its limitations, and exploring new materials and post-processing techniques.
Current Research and Developments in Binder Jetting
Researchers and industry experts are continuously working to improve binder jetting technology. They are exploring ways to enhance resolution, optimize material performance, and develop new post-processing methods to streamline production.
Challenges and Opportunities for Binder Jetting
While binder jetting holds immense promise, it also faces challenges that need to be addressed. Some of these include improving surface finish, increasing material options, and optimizing the overall process. However, with each challenge comes an opportunity for growth and innovation in this constantly evolving field.
Conclusion
Binder jetting is an exciting and promising evolution in the world of 3D printing. With its ability to print faster, work with diverse materials, and cater to a wide range of industries, it offers a host of advantages. While there are still areas to be explored and improved, the future of binder jetting looks bright. As technology continues to advance, it is only a matter of time before binder jetting becomes a staple in the manufacturing industry, driving innovation and transforming the way we produce objects.