Fused Deposition Modeling (FDM) is a highly popular additive manufacturing technology used for prototyping and production. This process creates models and parts by extruding thermoplastic materials layer by layer until the desired shape is formed.
Introduction to Fused Deposition Modeling (FDM)
Invented by S. Scott Crump in 1988, Fused Deposition Modeling (FDM) was initially developed as a tool to manufacture plastic injection molds. Over time, the technology has evolved and today FDM is one of the most popular and widely used 3D printing technologies in the world.
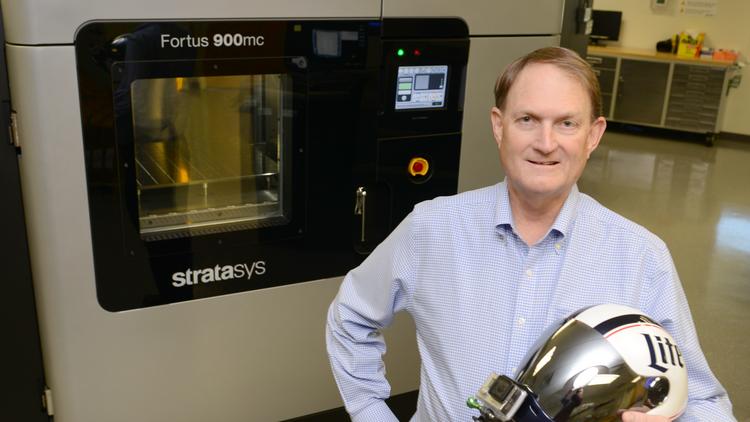
The History of FDM
The idea for FDM came to Crump when he was making a toy frog for his daughter using a glue gun and a mixture of polyethylene and candle wax. Crump realized he could use the same concept to build three-dimensional objects, and thus FDM was born.
The first FDM prototype was created in 1988 and was called the "Fused Deposition Modeling" machine. The machine was designed to print thermoplastic parts by melting plastic material and depositing it layer by layer. In 1990, the first FDM machine was sold, and by the early 2000s, FDM was widely adopted by many industries.
Today, FDM is used in a variety of industries, including aerospace, automotive, healthcare, and education.
How FDM Fits into the World of 3D Printing
3D printing involves the creation of a three-dimensional object from a digital model by adding layers of material. FDM is a specific type of 3D printing technology that uses a thermoplastic filament as the build material. The filament is melted and then extruded through a nozzle, layer by layer, to create the final product.
FDM is known for its versatility, as it can print a wide range of materials, including ABS, PLA, nylon, and polycarbonate. Additionally, FDM printers are widely available and are generally more affordable than other types of 3D printers.
However, FDM does have its limitations. It can be difficult to achieve high levels of detail and accuracy with FDM, and the layer lines can be visible on the final product.
Despite these limitations, FDM remains a popular choice for 3D printing enthusiasts and professionals alike. With the continued development of FDM technology, it is likely that we will see even more innovative uses for this versatile 3D printing technology in the future.
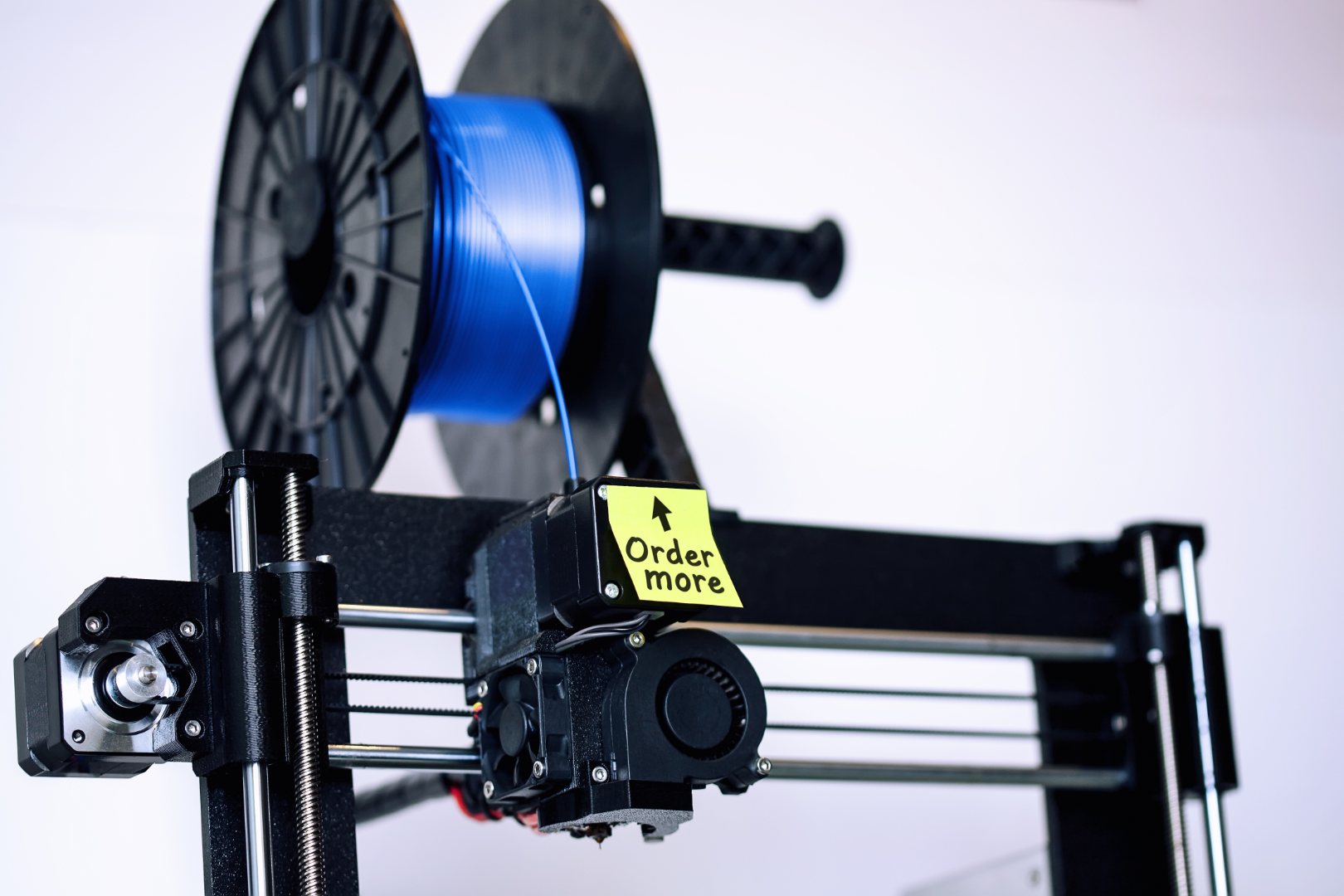
The FDM Process Explained
3D printing has revolutionized the way we create objects, and Fused Deposition Modeling (FDM) is one of the most popular 3D printing technologies. FDM printing is a process of building objects layer by layer using thermoplastic materials. This technology is widely used in various industries, including aerospace, automotive, and healthcare.
Key Components of an FDM Printer
An FDM printer consists of various components such as a print bed, extruder, nozzle, and filament. The print bed is where the object is printed. It can be heated or unheated, depending on the material being used. The extruder is responsible for pushing the filament through the hot end and out of the nozzle. The filament is melted in the hot end and deposited onto the print bed to create the object. The nozzle size can vary depending on the required resolution of the print.
Step-by-Step Guide to FDM Printing
The process of FDM printing begins with creating a 3D design on a computer. This design can be created using various software, including CAD (Computer-Aided Design) software. Once the design is complete, it is saved as an STL file. The STL file is imported into a slicing software that slices the model into layers. The slicing software then generates a G-code file that is read by the FDM printer to create the object.
Before printing, the FDM printer needs to be calibrated to ensure that the print bed is level and the extruder is at the correct height. The FDM printer heats up the extruder and the print bed to the required temperature and places the first layer of material. The printer continues to print layer by layer, following the G-code instructions, until the object is complete. The printing time can vary depending on the size and complexity of the object.
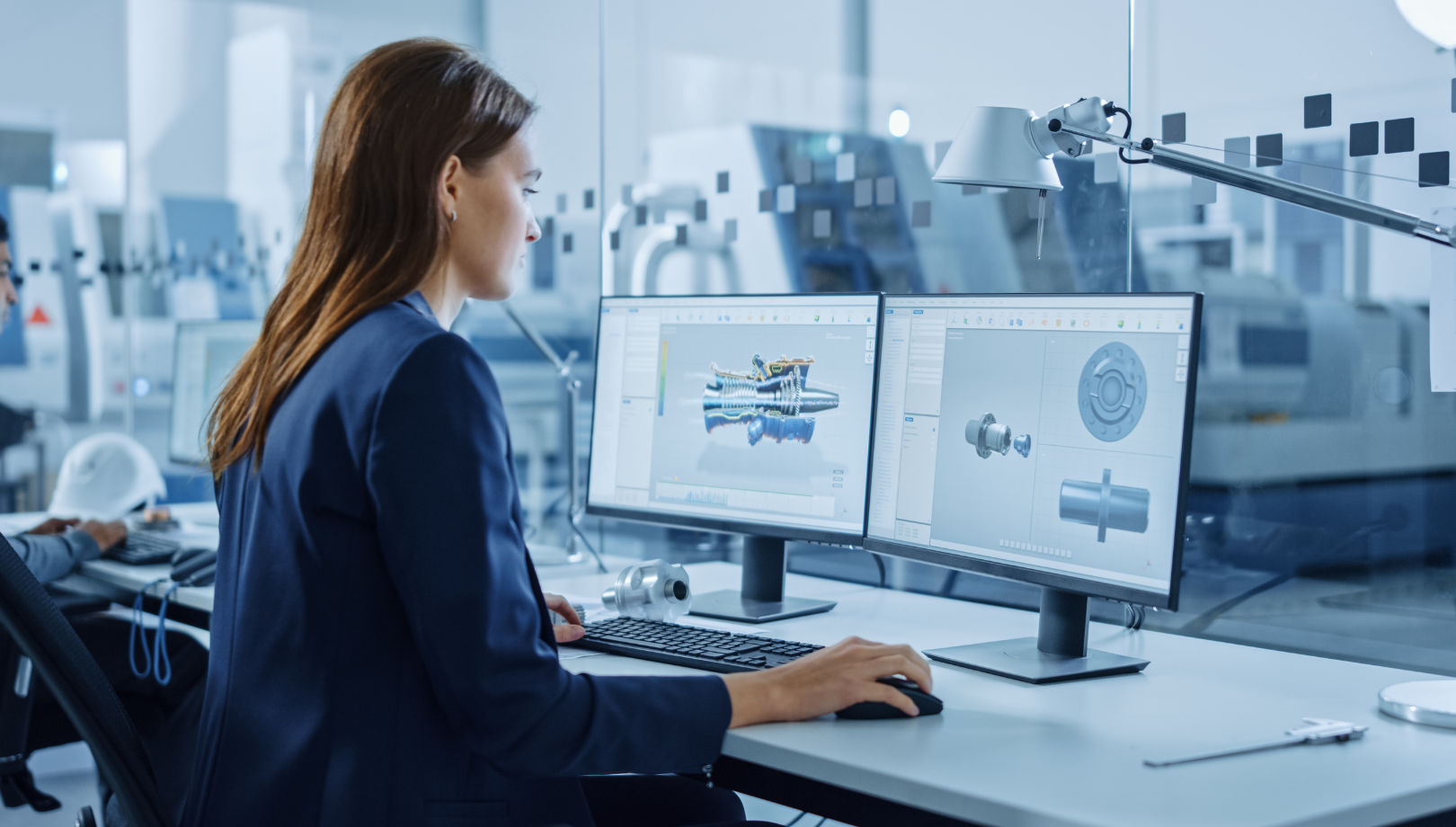
Understanding FDM Materials
FDM supports a wide range of thermoplastic materials, including PLA, ABS, PETG, and Nylon. PLA (Polylactic Acid) is a popular material for beginners and is easy to print with. It is a biodegradable material made from renewable resources such as corn starch. ABS (Acrylonitrile Butadiene Styrene) is stronger and more durable than PLA, making it a popular choice for engineering applications. PETG (Polyethylene Terephthalate Glycol) is known for its durability and flexibility and is commonly used in the 3D printing of mechanical parts. Nylon is a popular choice for high-stress applications due to its strength and toughness.
When selecting a material for FDM printing, it is important to consider the properties of the material and the requirements of the object being printed. Factors such as temperature resistance, flexibility, and strength should be taken into account.
Overall, FDM printing is a versatile and cost-effective 3D printing technology that can be used in various industries. With the ability to print objects with complex geometries and a wide range of materials, FDM printing is a valuable tool for prototyping, manufacturing, and research and development.
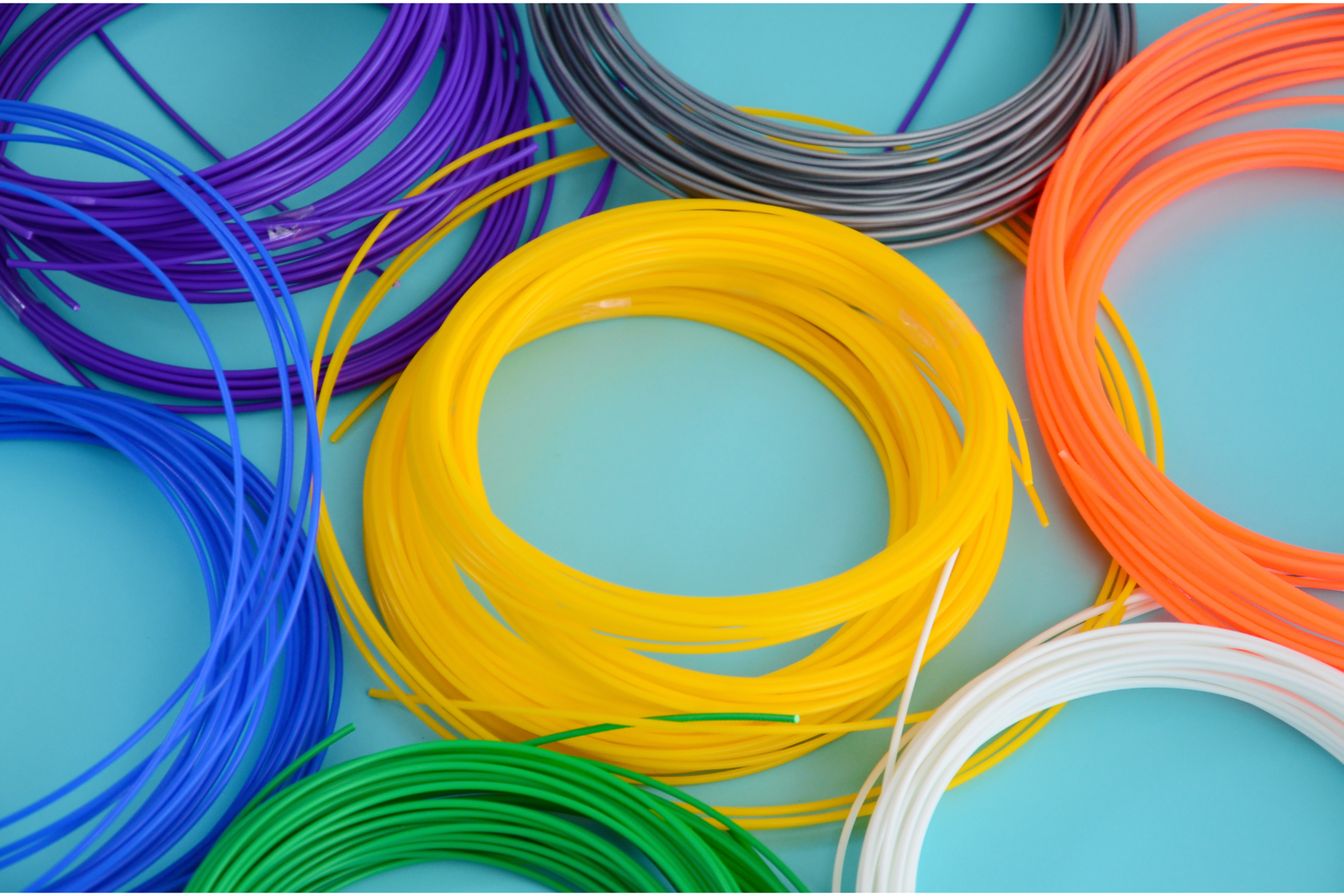
Advantages and Disadvantages of FDM
Benefits of FDM Technology
Fused Deposition Modeling (FDM) printing technology is a popular choice for 3D printing enthusiasts worldwide. This technology provides several benefits, including affordability, sustainability, and flexibility.
Affordability is one of the biggest advantages of FDM technology. It requires less expensive hardware and material costs than other 3D printing technologies, which makes it ideal for small businesses and individuals. The cost-effectiveness of FDM technology has made it accessible to a wider audience, enabling more people to experience the benefits of 3D printing.
FDM is also sustainable since it uses recyclable materials that can be reused and recycled. This feature makes it an environmentally friendly option for those who are conscious of their carbon footprint. The use of recyclable materials has also made FDM technology a popular choice in the manufacturing industry, where sustainability is a top priority.
The flexibility of FDM technology enables users to produce parts of almost any shape and size, making it an incredibly useful tool for prototyping. This feature has made it a popular choice for architects and engineers who require complex designs for their projects. FDM technology has also been used in the medical industry to produce prosthetic limbs and other medical devices.
Limitations and Challenges of FDM
Despite its many advantages, FDM technology also has some limitations and challenges that need to be considered. One of the main limitations of FDM is the build size, which makes it challenging to produce large-scale objects. This limitation has made it less popular in the manufacturing industry, where large-scale production is often required.
FDM products can also have visible layer lines, which can affect the aesthetic finish of the final product. Although this can be minimized with post-processing techniques, it can still be a challenge for those who require a smooth finish for their products.
The process can also be subject to warping or shrinkage of the material during printing, which can affect the final product's accuracy. This challenge has made it difficult to produce parts with high precision and accuracy, making it less popular in industries where precision is critical.
Applications of Fused Deposition Modeling
Rapid Prototyping with FDM
FDM has revolutionized the prototyping process in many industries by enabling designers to create rapid prototypes. The technology provides a quick turnaround time, which allows designers to iterate and refine designs at a much faster rate than traditional methods.
End-Use Parts and Manufacturing
FDM technology is also used for end-use parts and manufacturing. With the advances in materials and printer capabilities, FDM can produce high-quality parts that meet industry-grade standards. This approach can result in more efficient manufacturing processes, quicker delivery times, and reduced production costs.
Customization and Personalization
FDM technology provides an amazing degree of personalization to products by allowing for customization of design and color options. This feature is used by various industries such as fashion, jewelry, and automotive. FDM technology allows for customization processes and carries with it the benefits of reduced waste, faster production times, and product uniqueness.
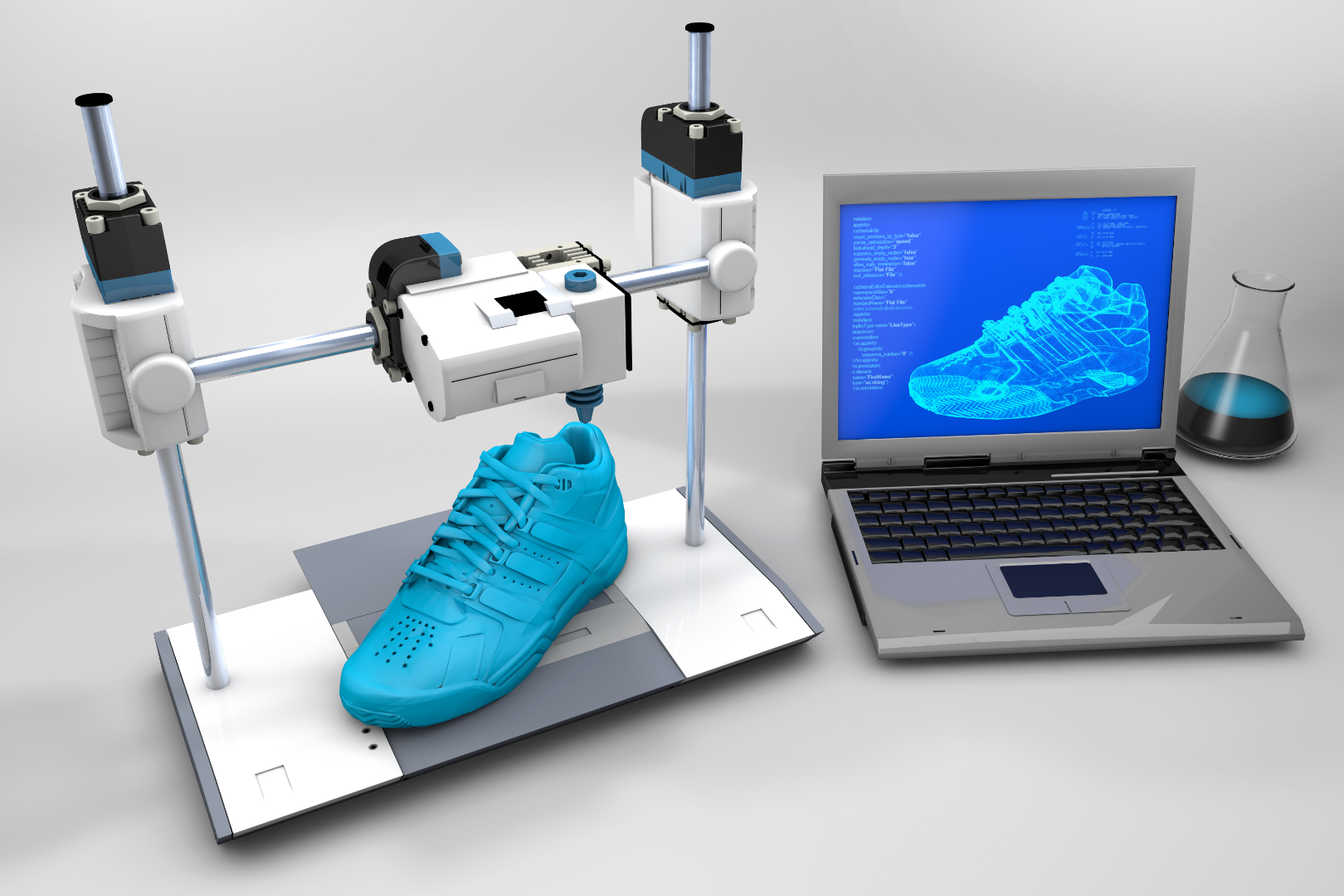
Comparing FDM to Other 3D Printing Technologies
FDM vs. Stereolithography (SLA)
Stereolithography uses a process of curing a photosensitive resin with UV light to form objects. It offers a high level of detail and accuracy compared to FDM and is best suited for small complex objects. Stereolithography is more expensive than FDM, and the resin can be expensive, limiting the range of applications.
FDM vs. Selective Laser Sintering (SLS)
SLS is a 3D printing technology that melts a powdered material with a laser to form objects. The process results in high strength and durability products, making it ideal for applications in engineering and manufacturing. SLS is considerably more expensive than FDM technology, requires higher temperatures, and is more complex, making it more difficult to operate and maintain.
FDM vs. Digital Light Processing (DLP)
Digital Light Processing or DLP uses photopolymer materials that are cured by UV light to produce 3D objects. DLP technology offers a high level of detail and accuracy compared to FDM but is limited in the range of materials it can use. DLP requires a high level of control during the printing process and can be expensive to operate and maintain.
The Future of Fused Deposition Modeling
FDM technology will continue to improve, and new materials will be developed to meet the requirements of different applications. As machines become more sophisticated, the range of possibilities will expand with the technology.
In conclusion, Fused Deposition Modeling (FDM) is an incredible technology that has transformed the world of manufacturing and production. With its ability to produce high-quality prototypes, end-use parts, and customization options, the future seems promising for FDM technology.