The world of construction is rapidly evolving, and 3D printing technology is among the most promising innovations. This technology has been used to produce everything from prosthetic limbs to airplane parts, and now, it's making its way into the housing sector. So, will 3D printed houses revolutionize the industry and become mainstream? In this article, we will explore the current state of 3D printed housing, the challenges and limitations, the technological advancements, and the potential impact on the construction industry.
The Current State of 3D Printed Housing
The world's first 3D printed house was built in China in 2014 using a giant 3D printer. Since then, several companies have emerged in the industry, such as Contour Crafting, Winsun, and Apis Cor. They have successfully 3D printed houses, apartments, and even commercial buildings with the use of robotic arms and various printing materials such as concrete, clay, and plastic.
3D printing can offer many advantages over traditional construction methods, including faster production, reduced waste, and improved precision. The use of 3D printing technology can cut the construction time by up to 70% and reduce construction waste by up to 60%. Additionally, the precision of 3D printing is so high that it can print complex designs and curves that are impossible to achieve with traditional building techniques.
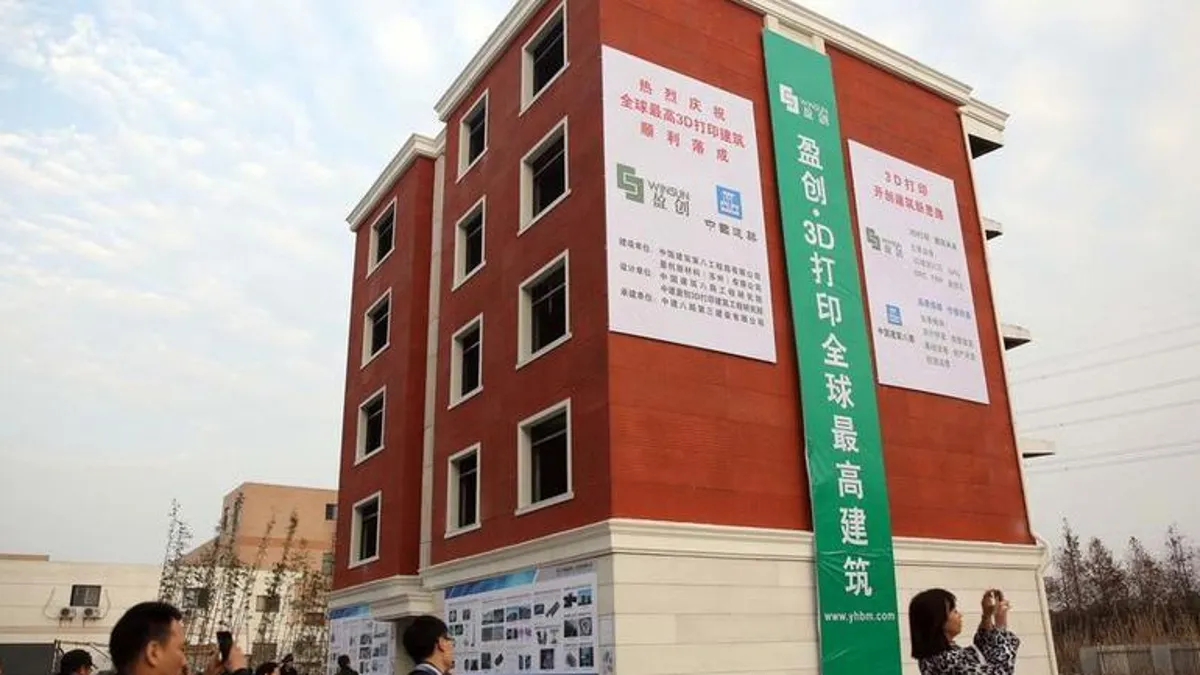
Pioneering Companies in the Industry
Contour Crafting, a company established by Dr. Behrokh Khoshnevis, has been at the forefront of the 3D printing industry. Its mission is to automate construction with its proprietary 3D printing technology, which can print structures up to 2,500 square feet in less than 24 hours. Winsun, a Chinese company, has also gained recognition for its 3D printed houses, hotels, and offices. It uses recycled building materials such as cement and glass fibers to produce durable and eco-friendly homes.
Another notable company is Mighty Buildings, a California-based startup that uses 3D printing to produce modular homes. The company has developed a unique thermoset composite material that is stronger and more sustainable than traditional building materials. The material is also fire-resistant and has superior insulation properties.
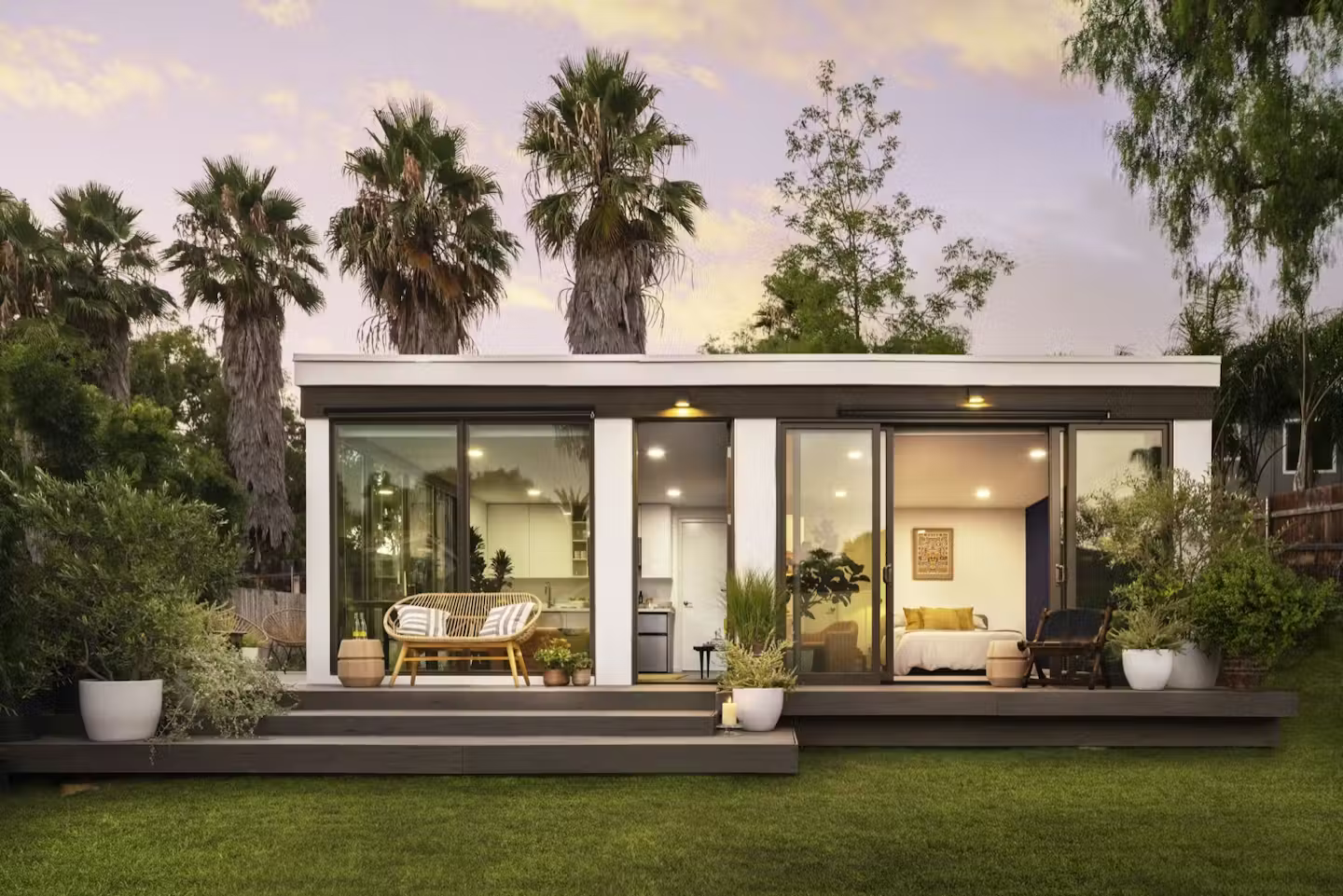
Notable 3D Printed Housing Projects
It's fascinating to see the myriad of projects accomplished in the 3D printing industry. In 2019, Icon, a startup based in Texas, 3D printed a house in less than 24 hours for a mere $10,000. By the end of that year, they had completed a small community of homes for low-income families in Mexico, all produced with their revolutionary Vulcan II printer. Similarly, in Dubai, the government has plans to 3D print 25% of its buildings by 2030, with one of the notable structures completed being an office building created by Apis Cor.
Another impressive project is the 3D printed house in Nantes, France. The project, led by the University of Nantes, used a robot to 3D print a house in just 18 days. The house is made of a bio-sourced material that is composed of 80% plant-based materials and 20% mineral-based materials.
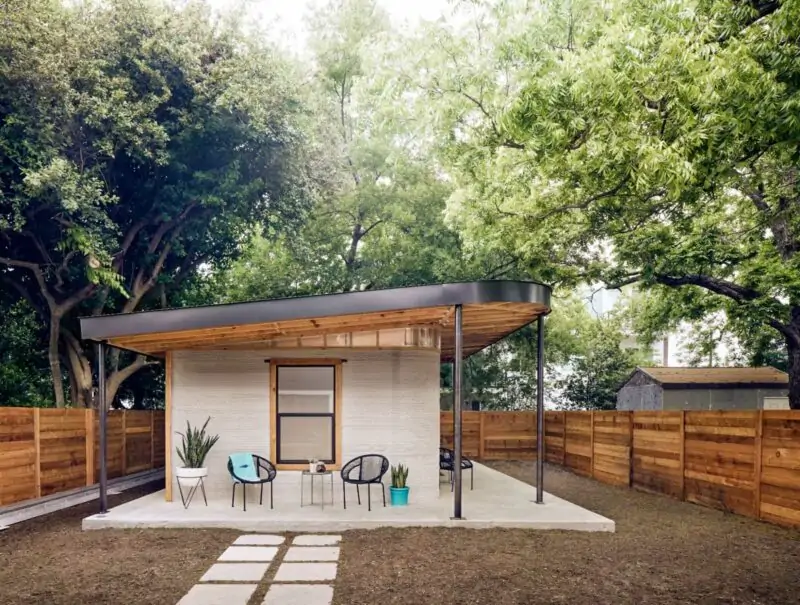
Advantages of 3D Printed Houses
3D printing technology can revolutionize the construction industry, but what are the advantages of 3D printed houses? The first significant advantage is speed. With 3D printing, a house can be constructed in days, instead of weeks or even months. Additionally, 3D printing is eco-friendly as it reduces waste, transports less material, and uses sustainable materials. Finally, 3D printed houses can be much cheaper than traditional houses since it eliminates the need for carpenters, welders, and other traditional laborers.
Another advantage of 3D printed houses is the ability to customize designs easily. With 3D printing, architects and designers can create unique and intricate designs that would have been impossible to achieve with traditional construction methods. 3D printing also allows for the creation of modular homes that can be easily assembled and disassembled, providing flexibility for homeowners.
Challenges and Limitations
Although 3D printed housing is becoming more prevalent, there are still several challenges and limitations to the technology. First, 3D printed houses are still relatively limited in size. Most 3D printed houses are small and designed for single-family use. Second, the printing material used has to be strong enough to withstand the elements and other stress tests. Third, there is still a limited range of materials available for 3D printing. Finally, the technology is still costly, and not all companies have resources or access to 3D printing equipment.
Another challenge is the lack of regulations and building codes for 3D printed houses. As the technology becomes more widespread, governments and regulatory bodies will need to establish guidelines and standards for 3D printed construction. This will ensure that 3D printed houses are safe, durable, and meet the same standards as traditional houses.
Despite these challenges, the future of 3D printed housing looks promising. With the continued development of new materials and technology, 3D printed houses could become the norm in the construction industry, providing affordable and sustainable housing for people around the world.
The Future of 3D Printed Housing
It's clear that 3D printed housing technology has the potential to revolutionize the construction industry as we know it. But what does the future hold?
Technological Advancements and Innovations
New materials, upgrades to printer technology, and automation will all contribute to a more efficient and effective method of 3D printing housing. Researchers are currently exploring the use of new materials such as wood and bioplastics, which can diversify the industry. Additionally, automation is being researched to streamline the printing process and further reduce the amount of labor required in the construction process.
One of the most exciting developments in 3D printing technology is the ability to print entire houses in a single day. This has been made possible by the development of larger 3D printers that can print at a faster rate. This means that the construction process can be completed in a fraction of the time it would take using traditional building methods.
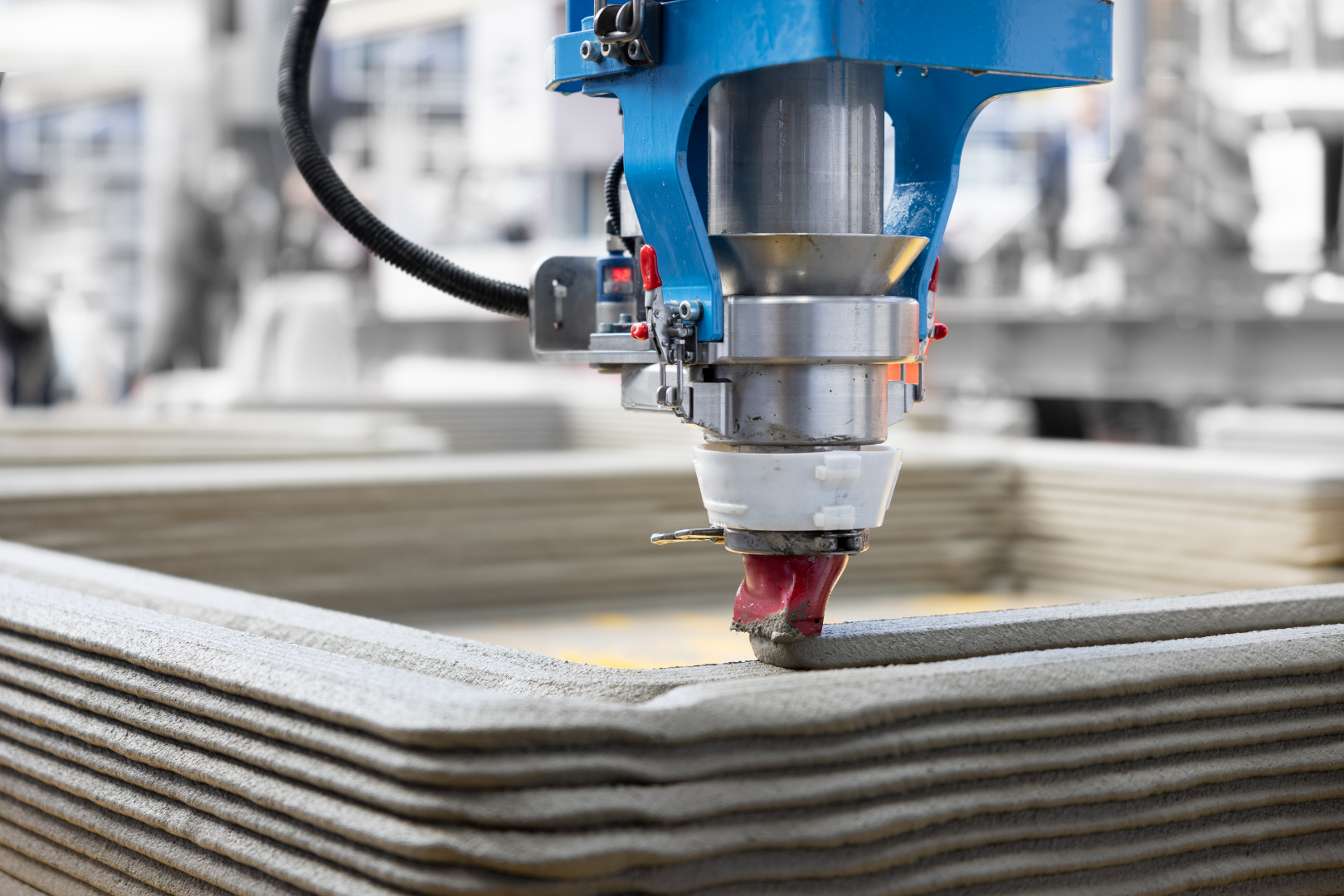
Potential Impact on the Construction Industry
3D printed housing technology has the potential to disrupt the construction industry in a way that hasn't been done before. Given its fast and cost-effective nature, it could reduce the labor required to construct a house or a building, thereby reducing costs. The technology can also create job opportunities for individuals trained in operating and managing 3D printers.
Another potential impact of 3D printed housing technology is the ability to construct buildings in hard-to-reach areas. This could be particularly useful in disaster zones or remote areas where traditional building methods are not feasible. The technology could also be used to construct buildings on other planets, such as Mars, where traditional building materials are not available.
Environmental Implications
The potential for sustainable building practices is one of the most exciting things about 3D printing. With the ability to use eco-friendly materials and reduce waste, it could help make the construction industry more sustainable and reduce its carbon footprint.
Additionally, 3D printed housing technology can be used to create buildings that are more energy-efficient. This is because the technology allows for the creation of intricate designs that can optimize the use of natural light and ventilation. This can help reduce the amount of energy required to heat and cool a building.
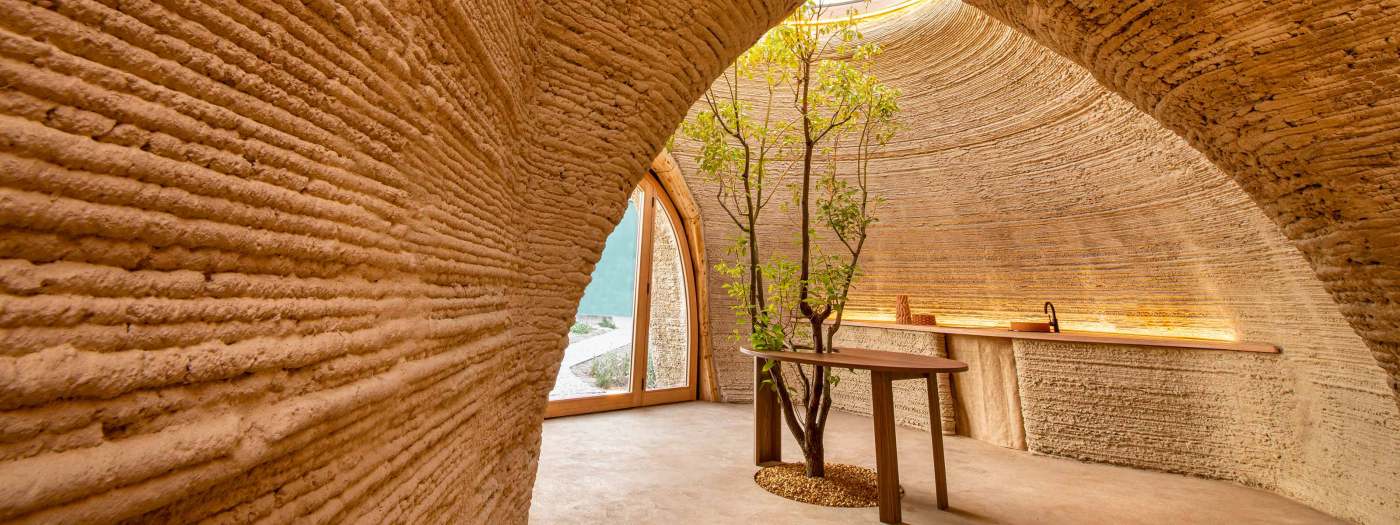
Affordability and Accessibility
The potential to construct more affordable and accessible housing is another exciting aspect of 3D printing technology. If there is broad adoption of a technology that can help provide housing solutions to people in need, it could have a profound impact on societies and economies worldwide.
Furthermore, 3D printed housing technology can be used to create customized housing solutions for individuals with disabilities. This could help improve their quality of life and allow them to live more independently.
Factors Influencing Mainstream Adoption
For 3D printed housing to become mainstream, several factors must be taken into consideration, including government policies and regulations, public acceptance, industry collaboration and partnerships, and economic viability and market demand.
Government Policies and Regulations
As with any new industry, government regulations play a crucial role in the 3D printed housing industry's growth and development. Policies need to be in place to ensure the safety and structural integrity of the 3D printed homes. Governments will need to work closely with 3D printing companies to establish these regulations and set standards.
Public Perception and Acceptance
The public's acceptance of 3D printed housing technology is also an important consideration. There will need to be a change in perception towards 3D printing, from being viewed as a novelty technology to something practical and useful. Education and awareness campaigns can help with this change in perception. Moreover, the technology must prove that it is reliable, safe, and durable.
Industry Collaboration and Partnerships
Collaboration and partnerships are essential in the growth of the 3D printed housing industry. Companies must share knowledge and innovations to accelerate the growth of the industry. Collaboration between companies and the government can also ensure that policies and regulations are aligned with industry needs.
Economic Viability and Market Demand
Finally, the economic viability of 3D printed housing technology and market demand is essential for widespread adoption. Companies must demonstrate that 3D printed houses are more cost-effective than traditional construction methods. Similarly, there must be a market demand for 3D printed houses by homeowners and real estate developers.
Conclusion
With the rapid growth of 3D printing technology, it's clear that 3D printed housing will become common in the near future. However, for it to become mainstream, various factors such as government policies and regulations, public acceptance, industry collaboration and partnerships, and economic viability and market demand will all need to align. It's an exciting time for the construction industry, and 3D printing technology offers a glimpse into what the future may hold.