The aviation industry constantly strives to push boundaries and innovate, and one exciting area of exploration is the use of 3D printing technology to manufacture plane parts. With its ability to create complex structures and reduce production time, 3D printing has the potential to revolutionize aircraft manufacturing. In this article, we will delve into the world of 3D printing, understand its technology and materials, explore its benefits, and examine the challenges and limitations it faces in aviation. We will also take a closer look at real-life case studies to gain insights into successful implementations and learn from failed attempts.
Understanding 3D Printing Technology
Before we dive deeper into the possibilities of 3D printing airplane components, let's get acquainted with this groundbreaking technology. 3D printing, also known as additive manufacturing, is a process that builds objects layer by layer using computer-generated digital models. It differs from traditional manufacturing methods, which often involve subtractive processes like cutting or shaping materials. With 3D printing, the possibilities for design and innovation are virtually limitless.
Now that we have a basic understanding of 3D printing, let's explore the core elements that make this technology possible – the basics of 3D printing and the materials used.
The Basics of 3D Printing
At its core, 3D printing involves the layer-by-layer deposition of materials to create a three-dimensional object. The process starts with a digital design file that is created using computer-aided design (CAD) software. This design file is then sliced into thin layers, and the 3D printer follows these instructions to build the object layer by layer.
Each layer is carefully deposited, and the printer moves on to the next layer until the entire object is complete. This layer-by-layer approach allows for intricate and complex designs to be created with ease. From architectural models to medical implants, 3D printing has revolutionized the way objects are manufactured.
There are different methods of 3D printing, each with its own advantages and applications. Some common techniques include fused deposition modeling (FDM), stereolithography (SLA), and selective laser sintering (SLS). These methods differ in how they deposit or cure the materials and the types of materials they are compatible with.
Fused deposition modeling (FDM) is one of the most widely used 3D printing techniques. It works by extruding a thermoplastic filament through a heated nozzle, which then solidifies as it cools down. This method is known for its affordability and versatility, making it popular among hobbyists and professionals alike.
Stereolithography (SLA), on the other hand, uses a liquid resin that is cured with a UV laser or other light sources. The resin hardens when exposed to light, allowing for the creation of highly detailed and smooth objects. SLA is often used in industries such as jewelry making and dentistry where precision is crucial.
Selective laser sintering (SLS) involves the use of a high-powered laser that fuses powdered materials together to create solid objects. This method is compatible with a wide range of materials, including metals, plastics, and ceramics. SLS is commonly used in industries such as automotive and aerospace, where strong and durable parts are required.
.png)
Materials Used in 3D Printing
The materials used in 3D printing can vary greatly depending on the desired properties of the final object. For plane parts, it is crucial to use materials that possess high strength-to-weight ratios and can withstand the extreme conditions of flight. Some commonly used materials in aviation include carbon fiber composites, titanium alloys, and lightweight metals like aluminum.
Carbon fiber composites are known for their exceptional strength and lightness, making them ideal for aerospace applications. These materials are made by combining carbon fibers with a polymer matrix, resulting in a material that is both strong and lightweight.
Titanium alloys are another popular choice in aerospace manufacturing. These alloys offer high strength, excellent corrosion resistance, and good heat resistance. Titanium is also known for its biocompatibility, making it suitable for medical implants.
Lightweight metals like aluminum are widely used in aircraft construction due to their low density and high strength. Aluminum alloys offer excellent mechanical properties and are easy to work with, making them a preferred choice for various aircraft components.
However, the range of materials compatible with 3D printing continues to expand as researchers develop new techniques. Polymers, ceramics, and even biological materials have been successfully used in 3D printing, opening up new possibilities for aircraft manufacturing.
Polymers such as ABS (Acrylonitrile Butadiene Styrene) and PLA (Polylactic Acid) are commonly used in 3D printing due to their affordability and ease of use. These materials offer a good balance of strength and flexibility, making them suitable for a wide range of applications.
Ceramics, including zirconia and alumina, are used in 3D printing for their high-temperature resistance and excellent mechanical properties. These materials are often used in industries such as dentistry and aerospace, where heat resistance and durability are essential.
Biological materials, such as living cells and biocompatible polymers, have also found applications in 3D printing. This field, known as bioprinting, holds great promise for regenerative medicine and tissue engineering. Scientists are exploring the possibility of printing organs and tissues using a patient's own cells, which could revolutionize the field of transplantation.
.png)
The Evolution of Aircraft Manufacturing
Before we explore the specific benefits of 3D printing in aircraft manufacturing, let's take a step back and understand the traditional methods that have been used for decades.
Traditional Methods of Plane Part Production
For years, aircraft manufacturers have relied on traditional manufacturing methods such as machining, molding, and casting to produce plane parts. These methods involve subtractive processes, where excess material is removed or shaped to achieve the desired form. While these methods have proven effective, they can be time-consuming, costly, and limited in their ability to create complex geometries.
The Shift Towards 3D Printing
Recognizing the limitations of traditional manufacturing methods, the aviation industry has increasingly turned to 3D printing. This shift has been driven by the technology's ability to reduce costs, enhance efficiency, and offer unparalleled design freedom. With 3D printing, it is possible to create lightweight, intricately designed parts that were once deemed impossible to manufacture.
By embracing 3D printing, aircraft manufacturers can optimize the functionality and performance of their planes while minimizing weight, saving fuel, and reducing environmental impact.
Benefits of 3D Printed Plane Parts
Now that we have a solid understanding of 3D printing technology and its application in aircraft manufacturing, let's explore the specific benefits it brings to the industry.
Cost-Effectiveness of 3D Printing
One of the most significant advantages of 3D printing in aviation is its potential to reduce costs. Traditional manufacturing methods often involve high upfront tooling costs and time-consuming processes. In contrast, 3D printing eliminates the need for expensive molds, jigs, and fixtures, allowing for more cost-effective production. With 3D printing, manufacturers can produce parts on-demand, reducing inventory costs and streamlining supply chains.
Furthermore, the ability to consolidate multiple components into a single 3D-printed part eliminates the need for assembly and reduces labor costs. This shift towards additive manufacturing has the potential to revolutionize the cost structure of aircraft production.
Increased Efficiency and Speed
Another significant advantage of 3D printing is its ability to drastically reduce production time. Traditional methods often involve lengthy lead times for tooling and part production, leading to delays in aircraft assembly. In contrast, 3D printing allows for rapid prototyping and the production of complex parts in a fraction of the time.
Not only does this mean faster turnaround times for manufacturing, but it also allows for more agile design iterations and faster response to market demands. 3D printing enables manufacturers to quickly adapt their designs and produce customized parts efficiently.
Customization and Flexibility
One of the most exciting aspects of 3D printing in aircraft manufacturing is its ability to enable customization and flexibility. With traditional manufacturing methods, customization often comes at a high cost due to the need for specialized tooling or molds. In contrast, 3D printing allows for easy customization of parts without the need for additional tooling.
Manufacturers can easily modify designs to fit specific aircraft models or incorporate unique features that optimize performance. This flexibility opens up new possibilities for innovative design approaches and allows for the production of truly tailored aircraft components.
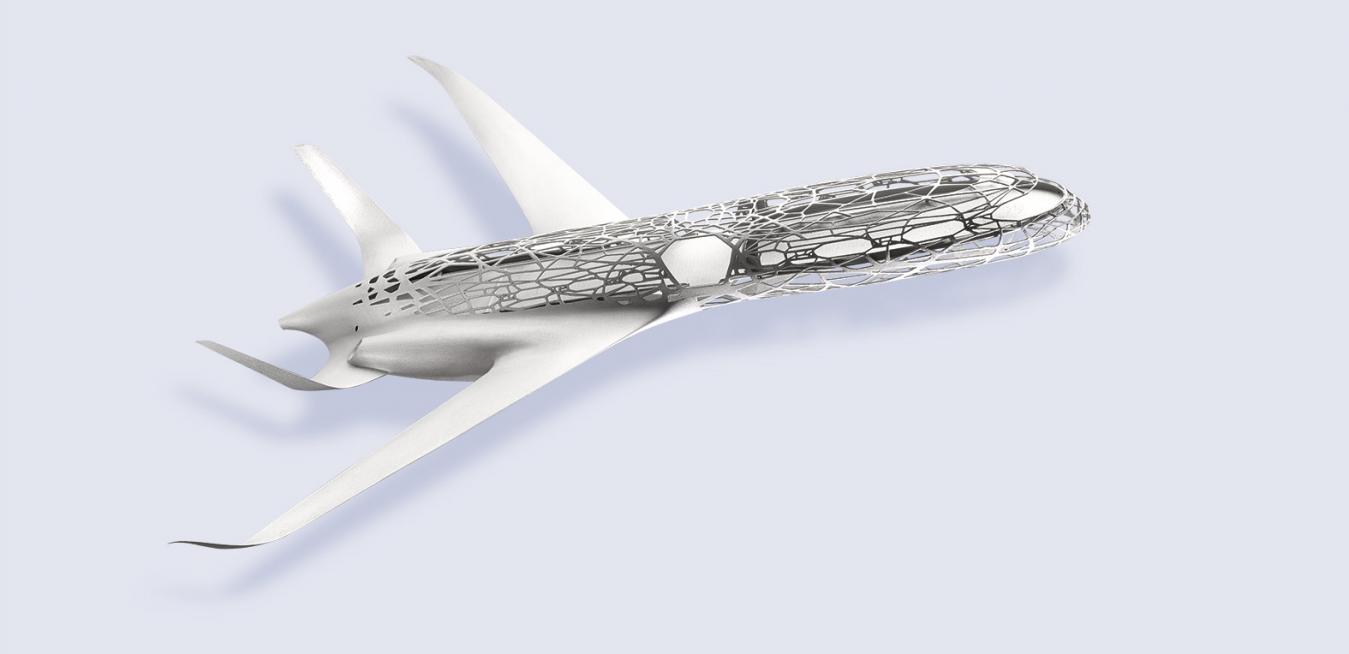
Challenges and Limitations of 3D Printing in Aviation
While the benefits of 3D printing in aviation are compelling, the technology also faces significant challenges and limitations that must be addressed for widespread adoption in the industry.
Quality Control and Standardization Issues
Ensuring the quality and consistency of 3D-printed parts remains a key challenge in aviation. Traditional manufacturing methods have well-established quality control processes and industry standards. In contrast, 3D printing is still relatively new, and standards and regulations are constantly evolving.
Manufacturers must work closely with regulatory bodies and invest in rigorous testing and inspection procedures to ensure the safety and reliability of 3D-printed airplane parts. Developing standardized quality control protocols will be crucial to gain industry-wide acceptance and build trust in the technology.
Regulatory and Safety Concerns
The aviation industry operates in a highly regulated environment, and any new technology must meet stringent safety standards. The adoption of 3D printing in aviation requires thorough validation and certification processes to ensure the parts meet the required performance and safety requirements.
Additionally, concerns related to the fire resistance and long-term durability of 3D-printed parts must be addressed. Extensive research and collaboration between manufacturers, regulatory authorities, and research institutions are essential to overcome these challenges.
Case Studies of 3D Printed Plane Parts
To gain deeper insights into the practical implications of 3D printing in aviation, let's examine a few real-life case studies that showcase both successful implementations and lessons learned from failed attempts.
Successful Implementations and Innovations
One remarkable example of successful implementation is the use of 3D printing to manufacture lightweight cabin components. Singapore Airlines partnered with Stratasys, a leading 3D printing solutions provider, to create customized cabin parts that are not only lightweight but also flame-retardant and compliant with industry standards.
Another notable case is the collaboration between Boom Supersonic and Stratasys to create the first 3D-printed metal flight hardware for supersonic aircraft. This partnership demonstrates the potential of 3D printing to transform the aerospace industry and enable the production of complex, high-performance parts at a fraction of the cost and time.
Lessons Learned from Failed Attempts
While 3D printing holds tremendous promise for the aviation industry, there have also been instances where the technology fell short. Airbus, for example, encountered challenges when attempting to 3D print titanium brackets for its A350 XWB aircraft. The complexity of the brackets and the limitations of the 3D printing process resulted in a significant number of rejected parts.
This case highlights the importance of thorough research, design optimization, and careful consideration of the limitations of 3D printing for each specific application. It serves as a reminder that successful implementation requires a deep understanding of the technology's capabilities and limitations.
Conclusion
The possibilities of 3D printed plane parts are vast and exciting. From enhancing efficiency and reducing costs to enabling customization and flexibility, 3D printing has the potential to revolutionize the aviation industry. However, to fully leverage its benefits, manufacturers must address challenges related to quality control, standardization, and regulatory compliance. With continued research, collaboration, and innovation, 3D printing in aviation will likely become more widespread, unlocking new opportunities for design and manufacturing in the years to come.