Der 3D-Druck revolutioniert die Art und Weise, wie Produkte entworfen und hergestellt werden. Eine der innovativsten und vielseitigsten Techniken in diesem Bereich ist das selektive Lasersintern (SLS). Durch die Nutzung der Leistung von Lasern und pulverförmigen Materialien hat sich SLS zu einem Wendepunkt in der 3D-Druckindustrie entwickelt.
Die Grundlagen des 3D-Drucks verstehen
Bevor wir uns mit den Feinheiten von SLS befassen, ist es wichtig, die Grundlagen des 3D-Drucks zu verstehen. Mit dieser revolutionären Technologie können Objekte auf der Grundlage digitaler Modelle Schicht für Schicht hergestellt werden. Im Gegensatz zu herkömmlichen Fertigungsverfahren, bei denen subtraktive Prozesse wie Bohren oder Schneiden zum Einsatz kommen, ist der 3D-Druck ein additiver Prozess, bei dem Materialien aufgebaut werden, um das Endprodukt zu formen.
Im Laufe der Jahre hat der 3D-Druck eine bemerkenswerte Entwicklung durchgemacht, von seinen bescheidenen Anfängen als Werkzeug für den Prototypenbau bis hin zu einer Technologie, mit der komplexe Strukturen mit bemerkenswerter Präzision hergestellt werden können.
Die Entwicklung des 3D-Drucks
Als der 3D-Druck in den 1980er Jahren aufkam, wurde er vor allem für das Rapid Prototyping eingesetzt. Designer und Ingenieure konnten ihre Ideen schnell in physische Prototypen umsetzen, was eine schnellere Iteration und Produktentwicklung ermöglichte. Diese bahnbrechende Innovation revolutionierte die Fertigungsindustrie und ermöglichte es Unternehmen, Zeit und Ressourcen im Produktentwicklungsprozess zu sparen.
Mit der Weiterentwicklung der Technologie fanden sich Anwendungen in verschiedenen Branchen, darunter Luft- und Raumfahrt, Automobilindustrie und Gesundheitswesen. In der Luft- und Raumfahrt wurde der 3D-Druck eingesetzt, um leichte und dennoch stabile Komponenten für Flugzeuge herzustellen, die den Treibstoffverbrauch senken und die Gesamtleistung verbessern. In der Automobilindustrie hat der 3D-Druck die Herstellung von kundenspezifischen Teilen und Prototypen ermöglicht, wodurch die Design- und Testphase beschleunigt wurde. Im Gesundheitswesen hat der 3D-Druck neue Möglichkeiten in der personalisierten Medizin eröffnet und die Herstellung von patientenspezifischen Implantaten und Prothesen ermöglicht.
Heute sind 3D-Drucker leichter zugänglich und erschwinglich geworden und haben den Weg für eine breite Akzeptanz und Innovation geebnet. Von kleinen Desktop-Druckern bis hin zu großen Industriemaschinen können Unternehmen und Privatpersonen jetzt die Leistung des 3D-Drucks nutzen, um maßgeschneiderte Produkte herzustellen. Diese Demokratisierung der Fertigung hat Unternehmern und Herstellern die Möglichkeit gegeben, ihre Ideen zu verwirklichen und eine Kultur der Innovation und Kreativität zu fördern.
Die wichtigsten Komponenten eines 3D-Druckers
Ein 3D-Drucker besteht aus mehreren wichtigen Komponenten, die zusammenarbeiten, um digitale Entwürfe in physische Objekte zu verwandeln. Das Verständnis dieser Komponenten ist für jeden, der die Welt des 3D-Drucks erkunden möchte, unerlässlich:
- Die Bauplattform: Dies ist die Plattform, auf der das Objekt Schicht für Schicht aufgebaut wird. Sie bietet eine stabile Grundlage für den Druckprozess und gewährleistet die Genauigkeit jeder einzelnen Schicht.
- Druckkopf oder Extruder: Der Druckkopf trägt das Material nach den Vorgaben des digitalen Designs auf oder extrudiert es. Er erhitzt das Material bis zu seinem Schmelzpunkt und steuert präzise den Materialfluss, so dass komplizierte Formen und Strukturen entstehen können.
- Steuersystem: Das Steuersystem koordiniert die Bewegungen und Vorgänge des Druckers, um einen präzisen Materialauftrag zu gewährleisten. Es interpretiert die digitale Entwurfsdatei und setzt sie in spezifische Anweisungen für die Motoren und den Extruder des Druckers um.
- Stromquelle: Die Stromquelle liefert die nötige Energie für den Betrieb der Druckerkomponenten, wie z. B. der Motoren und Heizelemente. Sie sorgt für eine stabile und gleichmäßige Stromversorgung, die einen unterbrechungsfreien Druckbetrieb ermöglicht.
- Filament oder Harz: Das für den 3D-Druck verwendete Material, ob Filament oder Harz, spielt eine entscheidende Rolle bei der Bestimmung der endgültigen Eigenschaften des gedruckten Objekts. Verschiedene Materialien bieten unterschiedliche Festigkeit, Flexibilität und Haltbarkeit und ermöglichen eine Vielzahl von Anwendungen.
- Software: Die beim 3D-Druck verwendete Software ist für die Erstellung und Bearbeitung digitaler Entwürfe sowie für deren Vorbereitung auf den Druck zuständig. Sie ermöglicht es den Nutzern, ihre Entwürfe zu bearbeiten und anzupassen und Parameter wie Größe, Ausrichtung und Fülldichte einzustellen.
Wenn man diese Schlüsselkomponenten versteht, kann man ein tieferes Verständnis für die Feinheiten des 3D-Drucks entwickeln und die grenzenlosen Möglichkeiten erkunden, die er in Bezug auf Design, Fertigung und Innovation bietet.
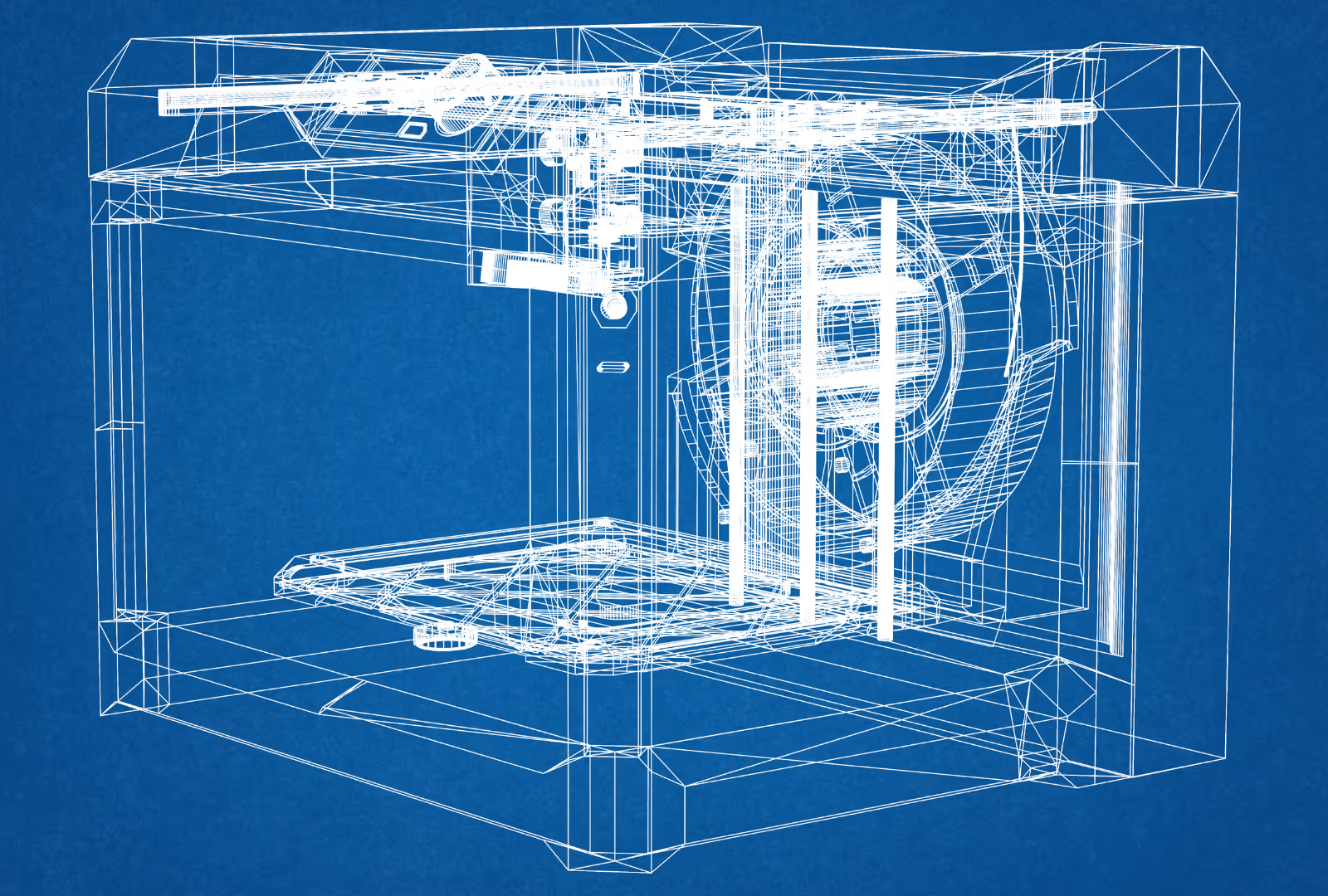
Einführung in das Selektive Laser-Sintern (SLS)
Nachdem wir nun die Grundlagen des 3D-Drucks kennengelernt haben, wollen wir uns nun mit den Besonderheiten des Selektiven Lasersinterns befassen. SLS ist ein 3D-Pulverbettdruckverfahren, bei dem Laser eingesetzt werden, um pulverförmige Materialien selektiv Schicht für Schicht zu verschmelzen und komplexe Objekte zu erzeugen.
Im Vergleich zu anderen 3D-Druckverfahren wie Fused Deposition Modeling (FDM) oder Stereolithographie (SLA) bietet SLS deutliche Vorteile in Bezug auf Vielseitigkeit und Materialeigenschaften.
Wie funktioniert SLS?
Beim SLS wird zunächst eine dünne Schicht aus pulverförmigem Material auf der Bauplattform verteilt. Ein Hochleistungslaser schmilzt oder sintert dann selektiv die Pulverpartikel zusammen und formt die gewünschte Form. Dann senkt sich die Bauplattform, und eine neue Pulverschicht wird aufgetragen, wobei der Prozess wiederholt wird, bis das gesamte Objekt hergestellt ist.
Der Einsatz von Lasern beim SLS ermöglicht eine präzise Steuerung des Fusionsprozesses, was zu äußerst präzisen und detaillierten Drucken führt. Darüber hinaus können selbsttragende Strukturen gedruckt werden, so dass keine Stützmaterialien erforderlich sind, was SLS ideal für komplizierte Designs macht.
Schauen wir uns das Verfahren genauer an. Wenn der Laser das pulverförmige Material abtastet, erzeugt er örtliche Hitze, wodurch die Partikel miteinander verschmelzen. Die Intensität und Dauer des Lasers werden sorgfältig gesteuert, um sicherzustellen, dass die richtige Wärmemenge zugeführt wird, was zu einer starken Verbindung führt. Wenn sich die Bauplattform absenkt, wird mit einer Walze oder einem Messer eine neue Pulverschicht aufgetragen, die für die nächste Runde des Laserscannens bereit ist. Dieser schichtweise Ansatz ermöglicht die Herstellung komplexer Geometrien und komplizierter Details, die mit herkömmlichen Fertigungsmethoden nur schwer zu erreichen wären.
Ein weiterer Vorteil von SLS ist die Fähigkeit, Objekte mit guten mechanischen Eigenschaften herzustellen. Durch die Verschmelzung der Pulverpartikel entsteht eine feste, dichte Struktur, die zu Teilen führt, die stark und haltbar sind. Dadurch eignet sich das SLS-Verfahren für eine Vielzahl von Anwendungen, darunter funktionale Prototypen, Teile für den Endverbraucher und sogar medizinische Implantate.
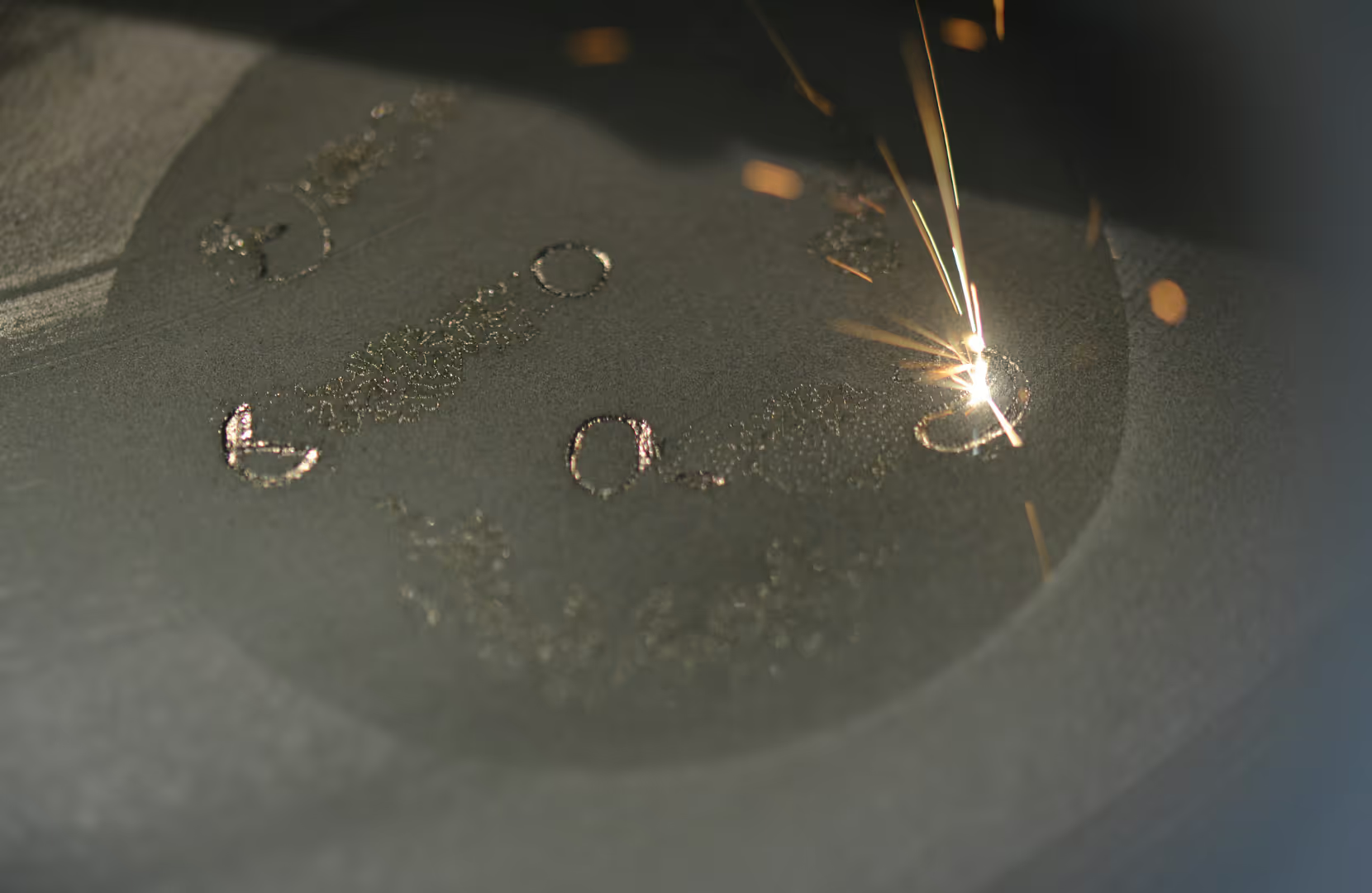
In SLS verwendete Materialien
Einer der größten Vorteile von SLS ist die breite Palette an kompatiblen Materialien. Im Gegensatz zu anderen 3D-Druckverfahren, die auf bestimmte Materialien beschränkt sind, kann SLS mit einer Vielzahl von Pulvern arbeiten, darunter Kunststoffe, Metalle und Keramiken.
Zu den beim SLS üblicherweise verwendeten Kunststoffen gehören Nylon, Polycarbonat und Polypropylen. Diese Materialien bieten hervorragende mechanische Eigenschaften und eignen sich daher für Funktionsprototypen und Endverbrauchsteile. Vor allem Nylon wird aufgrund seiner Festigkeit, Flexibilität und Hitzebeständigkeit häufig für SLS verwendet.
Auch Metallpulver wie Aluminium, Titan und Stahl können im SLS-Verfahren verwendet werden und ermöglichen die Herstellung von Metallteilen mit komplexen Geometrien. Dies eröffnet neue Möglichkeiten in Branchen wie der Luft- und Raumfahrt, der Automobilindustrie und dem Gesundheitswesen, in denen leichte und dennoch stabile Metallteile sehr gefragt sind.
Neben Kunststoffen und Metallen kann SLS auch mit Keramikpulvern arbeiten. Keramik bietet einzigartige Eigenschaften wie hohe Temperaturbeständigkeit, elektrische Isolierung und Biokompatibilität und eignet sich daher für eine Vielzahl von Anwendungen, darunter Elektronik, Luft- und Raumfahrt und medizinische Geräte.
Es sei darauf hingewiesen, dass die Wahl des Materials für SLS von den spezifischen Anforderungen der jeweiligen Anwendung abhängt. Faktoren wie mechanische Eigenschaften, thermische Stabilität, chemische Beständigkeit und Kosten spielen bei der Materialauswahl eine entscheidende Rolle.
SLS im Vergleich zu anderen 3D-Drucktechniken
SLS weist zwar Ähnlichkeiten mit anderen 3D-Druckverfahren auf, unterscheidet sich aber in Bezug auf seine Fähigkeiten und Anwendungen. Werfen wir einen genaueren Blick darauf, wie SLS im Vergleich zu Fused Deposition Modeling (FDM) und Stereolithographie (SLA) abschneidet.
SLS vs. Fused Deposition Modeling (FDM)
Bei FDM, einer der am häufigsten verwendeten 3D-Drucktechniken, werden geschmolzene thermoplastische Filamente extrudiert, um Objekte Schicht für Schicht aufzubauen. FDM ist zwar kostengünstig und leicht zugänglich, aber in Bezug auf die Oberflächenqualität und Materialkompatibilität begrenzt. SLS hingegen bietet eine bessere Oberflächenqualität und eine größere Materialvielfalt und eignet sich daher für ein breiteres Spektrum an Anwendungen.
SLS vs. Stereolithographie (SLA)
SLA basiert auf der Photopolymerisation zur Herstellung von Objekten durch selektives Aushärten von Flüssigharz mit einem UV-Laser. SLA erzeugt hochauflösende Drucke mit glatten Oberflächen, ist aber durch die Notwendigkeit von Stützstrukturen und die Verfügbarkeit kompatibler Harze eingeschränkt. SLS, das selbsttragende Strukturen drucken und mit einer größeren Vielfalt von Materialien arbeiten kann, überwindet diese Einschränkungen.
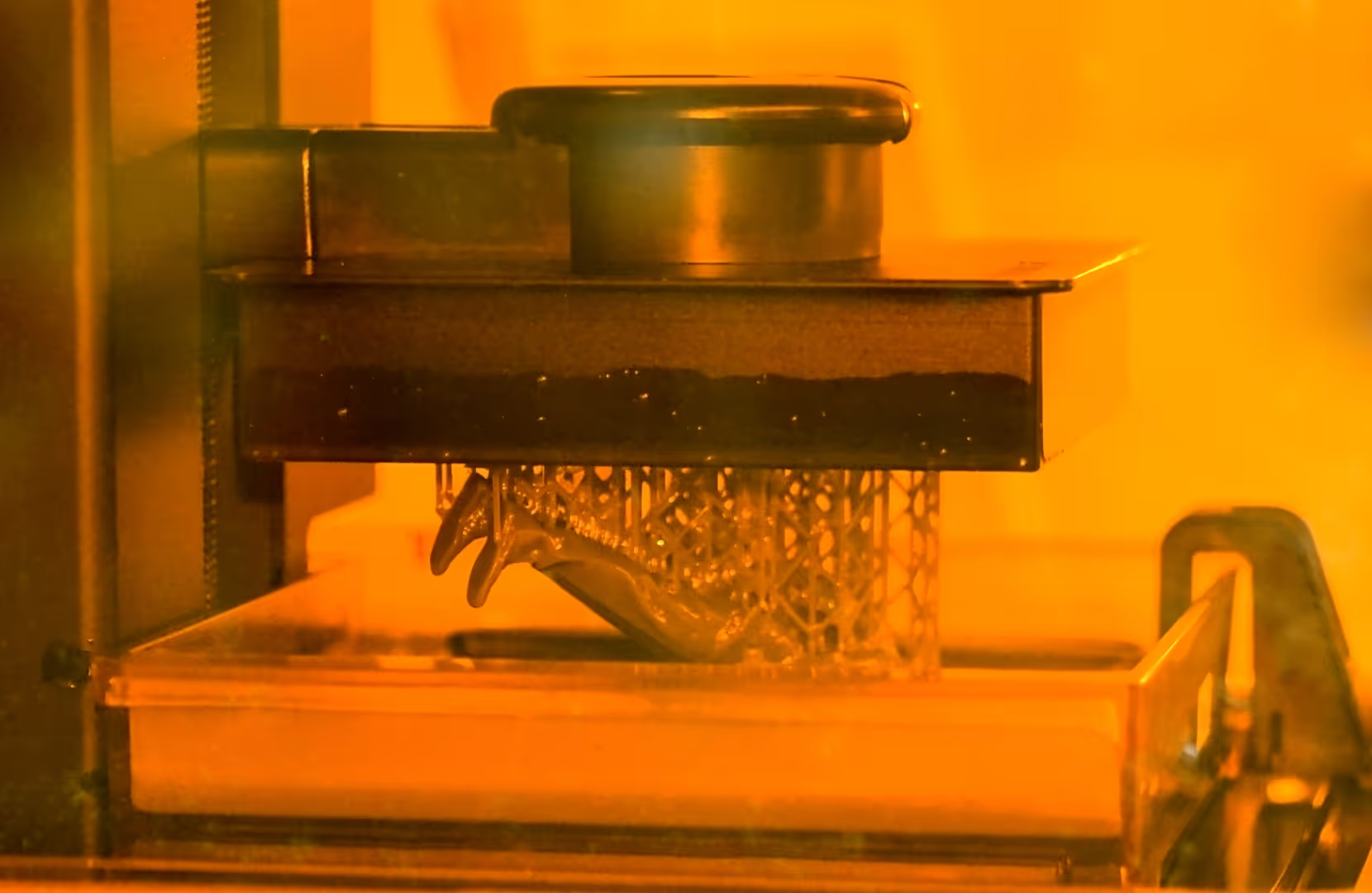
Die Vorteile des selektiven Lasersinterns
Nachdem wir nun das Innenleben von SLS und seinen Vergleich mit anderen 3D-Druckverfahren verstanden haben, wollen wir seine einzigartigen Vorteile erforschen, die es zu einem Wendepunkt machen.
Überlegene Details und Präzision
SLS liefert dank der Hochleistungslaser, die bei diesem Verfahren eingesetzt werden, außergewöhnliche Details und Präzision. Die Laser können eine Auflösung von bis zu 25 Mikrometern erreichen, was zu genauen und komplizierten Drucken führt. Dank dieses Präzisionsniveaus eignet sich SLS für Anwendungen, die enge Toleranzen und komplizierte Merkmale erfordern.
Größere Materialvielfalt
Im Gegensatz zu anderen 3D-Druckverfahren ist SLS nicht auf eine bestimmte Palette von Materialien beschränkt. Mit SLS ist es möglich, mit verschiedenen pulverförmigen Materialien zu arbeiten, was die Herstellung von Funktionsprototypen, Endverbrauchsteilen und sogar maßgeschneiderten Produkten ermöglicht. Diese Vielseitigkeit ermöglicht es Unternehmen und Designern, verschiedene Materialien zu erforschen und ihre Designs für bestimmte Zwecke zu optimieren.
Anwendungen von SLS in verschiedenen Branchen
Dank seiner einzigartigen Stärken findet SLS in verschiedenen Branchen Anwendung, bietet innovative Lösungen und verschiebt die Grenzen traditioneller Fertigungsverfahren. Lassen Sie uns einige Schlüsselbereiche erkunden, in denen SLS einen bedeutenden Einfluss hat.
SLS im medizinischen Bereich
SLS hat den medizinischen Bereich revolutioniert, indem es die Herstellung von maßgeschneiderten Prothesen, Orthesen und Implantaten ermöglicht. Die Möglichkeit, komplexe Geometrien zu drucken und patientenspezifische Designs zu integrieren, hat die Art und Weise, wie medizinische Geräte hergestellt werden, verändert. SLS erleichtert auch das schnelle Prototyping von chirurgischen Werkzeugen und anatomischen Modellen und ermöglicht so eine bessere chirurgische Planung und Ausbildung.
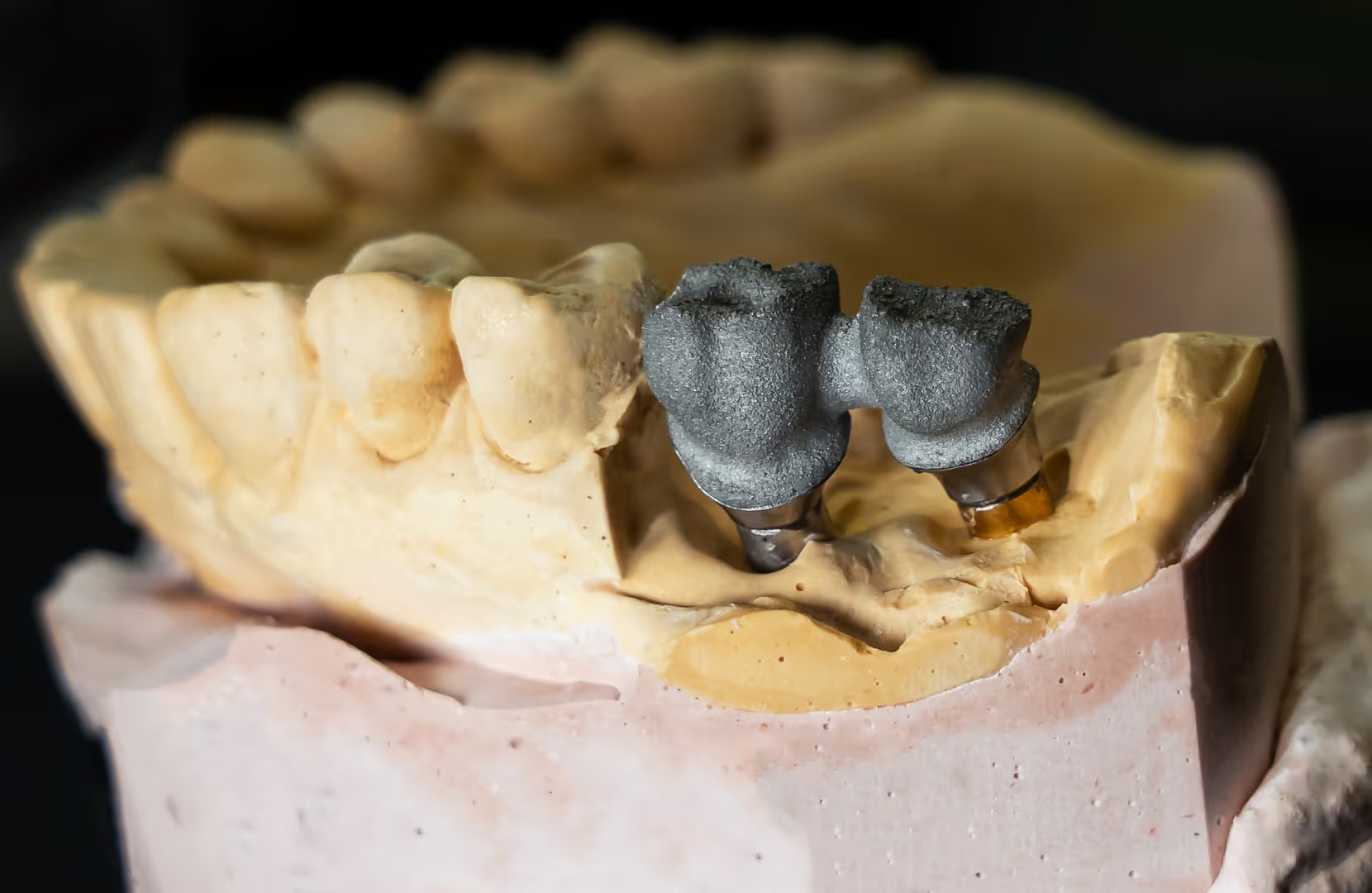
SLS in der Automobilproduktion
Die Automobilindustrie hat SLS wegen seiner Fähigkeit, leichte Komponenten mit komplizierten Designs herzustellen, für sich entdeckt. SLS ermöglicht die Herstellung komplexer Luftkanäle, konformer Kühlkanäle und funktionaler Prototypen, die Test- und Validierungsverfahren standhalten. Mit SLS können Hersteller ihre Werkzeugkosten senken, die Produktleistung verbessern und ihre Produktentwicklungszyklen beschleunigen.
Fazit
Das Selektive Lasersintern (SLS) hat sich in der 3D-Druckindustrie als bahnbrechende Neuerung erwiesen. Durch den Einsatz von Lasern und pulverförmigen Materialien bietet SLS eine hervorragende Detailgenauigkeit, Präzision und Materialvielfalt. Mit Anwendungen in verschiedenen Branchen erweitert SLS die Grenzen traditioneller Fertigungsverfahren. Im Zuge des technologischen Fortschritts und der Weiterentwicklung von Materialien ist SLS in der Lage, die Zukunft der Fertigung zu gestalten und den Weg für innovative und kundenspezifische Produkte zu ebnen.